Label Presses
JIN XIANG has 33 years of experience in designing and manufacturing letterpress printing machines, capable of providing 1-13 colors printing machines with optional web widths. Flexo press is suited for roll-to-roll printing, like plastic film (PET film, BOPP film), metal film and so on. Oil-based ink enables the printed products of full color and beautiful patterns. Due to the low cost of printing plate cylinder, different types of plate cylinders can be made to satisfy customers’ various demands. Our label presses are widely applied in label printing and flexible packaging printing industries.
The followings are some of our commonly produced label presses and you can order directly. Modifying or customizing is also available to suit your demands.
JIN XIANG is good at manufacturing flexographic printing machines for printing metallic labels, like iron and aluminum. Metal materials are heavier than flexible materials, so we design a feeding table with higher bearing capacity. To ensure the printing quality of metal materials, we recommend you to slow down the printing process. No exhaust gas is generated during the operation of our label presses, being environment-friendly.JIN XIANG flexo printing machine has features of high automation and simple operation. Only one or two operators are required for the printing operation, greatly saving labor cost.
In order to ensure the printing accuracy under long-term high speed operation, a tension controller is installed on the top of equipment. Operators adjust the tension according to the material and thickness of printing substrates.
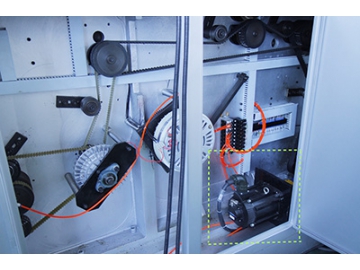
Only one main motor is required to power the whole equipment. Then the power is transferred to each printing unit precisely through the gearing, allowing all units with consistent and stable printing speed and producing more accurate printing effect. Our label press is driven by original Yaskawa servo motors.
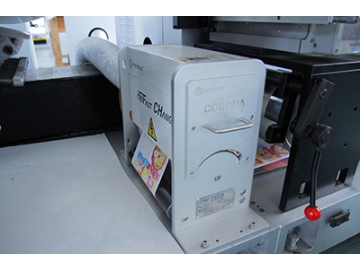
PVC, BOPP and other films are not easy for the ink to adhere due to the smooth surface, which affects the printing effect. Before printing, the corona treatment is helpful to enhance the adhesion of ink on materials, thus providing better printing effect. JIN XAING label press is ideal to print on various materials.
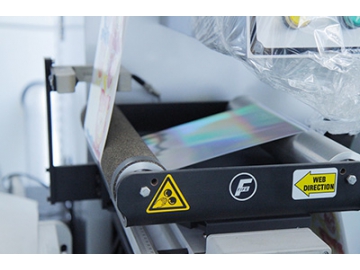
The original America FIFE web guide controller allows for more accurate printing. During material feeding, the materials are not aligned for long-term transferring and the generated slight vibration will also cause deviation of position, thus leading to poor printing effect. Web guide controller can be equipped to correct the lateral deviation of the printing material in its forward motion.
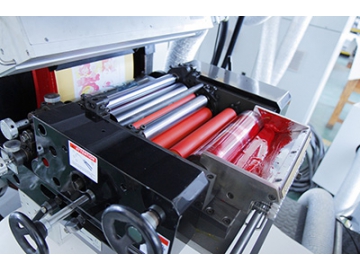
Each group of ink fountain roller contains 7 ink rolls. The ink is very sticky and direct inking will influence the printing effect. The process of ink distributing makes the ink to be adhered uniformly on the surface of printed materials.
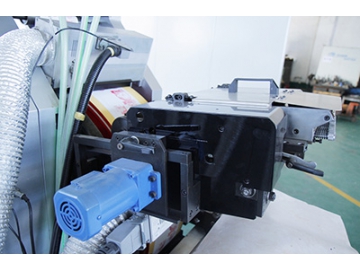
In changing ink, a scraper is needed to clean the ink on ink foundation roll so as to ensure precise printing color. Each printing unit equips an individual motor to drive the scraper for cleaning operation independently.
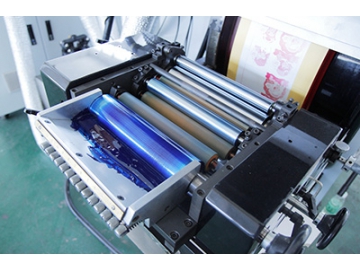
Manual inking is applied.
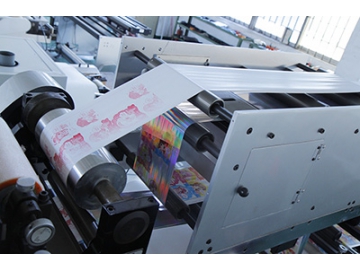
UV drying unit is commonly used. A power-saving LED drying is also optional. Due to the weak adhesion of dried ink, LED drying is not recommended for substrates requiring varnishing process.
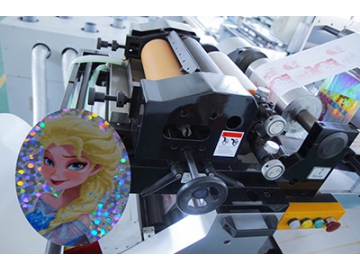
Varnishing unit is set after the printing unit, requiring the configuration of an UV drying unit. Varnishing offers more colorful and brighter printed pattern.
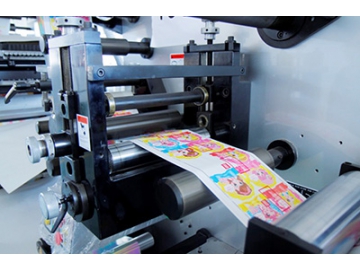
Die cutter can be installed to cut the waste of printed materials before rewinding operation.
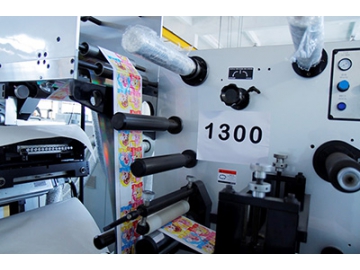
When the printing is finished and before rewinding, a protective layer can be laminated on this unit to protect the patterns from scratching.
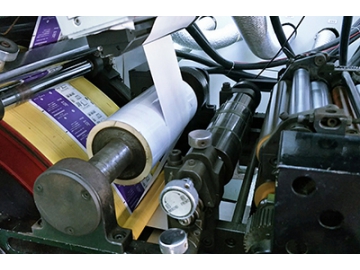
This unit performs the task of reverse printing.
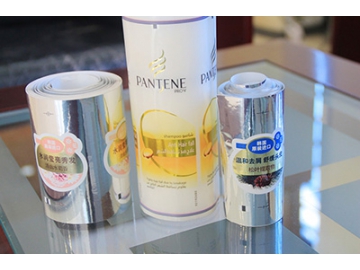
Ink cannot deploy metallic colors of golden and silver and gold ink costs a lot. Here the cold foil system is helpful to print metallic golden and silver patterns.
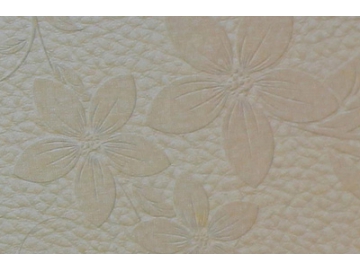
This printing unit offering materials of 3-D dimensional and embossing effect.
This accommodates to customers requiring gravure printing or digital printing.
Cutting off or into a required shape: it is ideal for customers to cut the printed material off or into different shapes.
Static observation system facilitate operators to check out the accuracy of patterns under high speed operating.
Materials like plastic film are easy to deform and even stick together after drying. So the cooling process is necessary.
Plastic film is easy to generate static during the printing process, causing operation obstruction and even accident. Electrostatic eliminator helps the material to achieve an ionizing balance (equality of positive and negative ions) to eliminate electrostatic.
Lamination unit is suitable for customers to fold the printed materials.