Small Scale Relocatable Modular Batch Gold Cyanide Leaching-Zinc Powder Displacement Plant
Small scale batch leaching plant is suitable for recovering gold from concentrates and high grade ores. Concentrates or high grade ores after flotation or gravity concentration are collected together for next processing.
Putting materials, steel balls and cyanide solutions to the ball mill and starting leaching while grinding. Meanwhile, remember to blow oxygen into ball mill at interval to compensate the oxygen consumption in the chemical reaction, greatly improving leaching efficiency. To control grinding fineness by customizing grinding time, ensuring the complete dissociation of gold and its reaction with cyanide.
When the fineness of slurry decreases, it is discharged from ball mill and continues to be mixed for next leaching in the leaching tank. After natural sediment for a period of time, the clarified production solution is discharged to filter press and then flows to production solution pool. Then adding poor fluid to leachign tank for next leaching and washing. Such a cycle needs to be repeated a few times while controlling each leaching time and washing time which will greatly improve gold leaching rate.
The purified production solution is sent to Merrill Crowe system of which zinc powder is used to displace solvent gold. The closed Merrill Crowe system is installed with a vacuum pump to discharge oxygen which can reduce the consumption of zinc and improve displacement efficiency as much as possible. The gold mud is naturally settled after the displacement reaction and poor fluid is discharged to poor fluid pool. Mass of gold mud will be discharged from displacement mixing tank with conic bottom where sulfuric acid is used to eliminate zinc and gold mud waits to be smelted and casted.
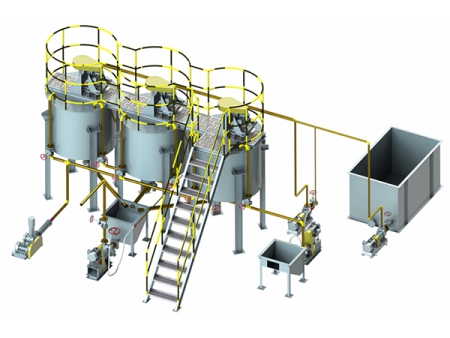
The ball mill has sealed structure designed for batch leaching. People can randomly add materials, cyanides, water and grinding ball to ball mill. The special inflation tube of ball mill regularly injects air to inner ball mill during grinding, ensuring sufficient oxygen content in the grinding chamber and the prompt reaction between exposed gold and cyanides. Thus the leaching capacity and efficiency are both enhanced.
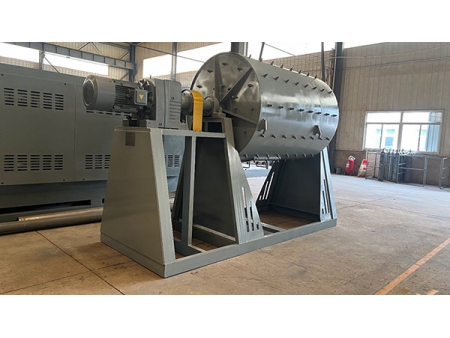
Inner space of this washing tank is installed with mixers and drain outlets at different height are installed on the surface of tank. Those outlets have double functions of mixing and washing. As each leaching ends, natural sediment follows. Gold content in the solution determines which height of drain outlet is selected to discharge production solution. Then poor fluid will be further added for leaching and washing.
Leaching efficiency is greatly improved because the solutions containing gold is promptly discharged and poor fluid is replenished.
A set of tanks need to be recycled because of batches of operation.
Purified production solution enters into the closed cylinder with conic bottom and mixer. As vacuum pump releases all the air in the cylinder, zinc powder is added to cylinder to displace gold which is settled at the conic bottom of cylinder. Sampling valve on the tank can test gold content in the solutions at any time to determine whether zinc needs to be added again. Natural sediment happens when the reaction stops and poor fluid is discharged.
This equipment, with simple structure and operation and over 99% of displacement efficiency, reduces zinc consumption and further decreases acid washing workload and acid consumption.
Grinding capacity of each batch:650kg
Total leaching time:24-48h
Leaching particle:-325mesh
Leaching-washing cycle number:3-4