Vertical Ribbon Mixer
Industrial blending machine for mixing solids, powders and pastes
S&L vertical ribbon mixer, also known as vertical mixer, ribbon blade mixer or ribbon blender, is an industrial blending equipment for mixing solids, powders and pastes. This high precision mixing equipment is especially suitable for mixing materials with various character like density, particle size and shape, proportions, and it offers good mixing effect even for a proportion as high as 1:100-10000.
The vertical ribbon blender consists of a vertical mixing spiral, initiating a three-dimensional flow to achieve a helical upward movement on the periphery and downward flow in the center.
S&L vertical ribbon mixer is suited for the mixing and blending of powders in a large number of industries, such as food, chemicals, bioproduct, cosmetic, battery, and so on.
S&L vertical ribbon mixer is ideal for mixing and blending of dry powders, solids, granule, as well as liquids and pastes (like paints), etc.
Pressure/vacuum blending, Reacting Agglomerating
Model | Length (mm) | Width (mm) | Volume (m³) | Weight (kg) | Power (kW) |
1800 | 950 | 0.07 | 350 | 3 | |
2100 | 1200 | 0.21 | 500 | 4 | |
2400 | 1300 | 0.35 | 650 | 7.5 | |
2500 | 1800 | 0.7 | 1150 | 11 | |
2900 | 2100 | 1.4 | 1850 | 15 | |
3200 | 2300 | 2.1 | 2150 | 22 | |
3500 | 2500 | 2.8 | 2600 | 30 | |
4500 | 2500 | 3.5 | 3500 | 37 | |
4900 | 2500 | 4.2 | 3850 | 37 | |
5100 | 2500 | 5.6 | 4500 | 45 | |
5550 | 2500 | 7 | 5400 | 55 |
-
Mixing system and cleanup door
The main mixing component is a vertical ribbon. The large side-opening door allows for easy and efficient cleaning. -
Drive unit
The drive unit and feeding port are arranged at the top, typically driven by a motor directly connected to a gear reducer. -
Pneumatic discharge
The pneumatic discharge outlet arranged at the bottom of the vessel ensures clean and efficient material discharge with minimal residue. -
Auxiliary mixer
The chopper arranged on the side of the vessel is directly connected to the motor, serving to assist in mixing and dispersing agglomerated materials. -
Spray nozzle
The spray pipe, which is inserted into the main shaft of the reducer, extends all the way into the center of the mixing shaft. The diagram shows a rotating joint at the inlet port. -
Spraying effect
The spray pipe connected from the hollow main spindle rotates with it, resulting in improved spraying effect of the atomizing nozzle.
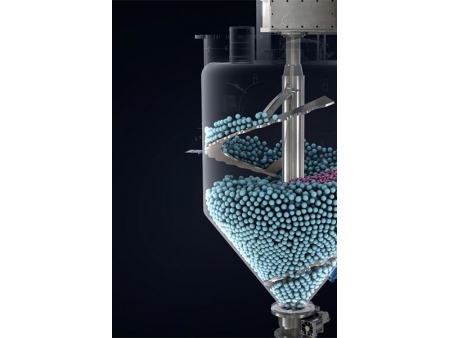
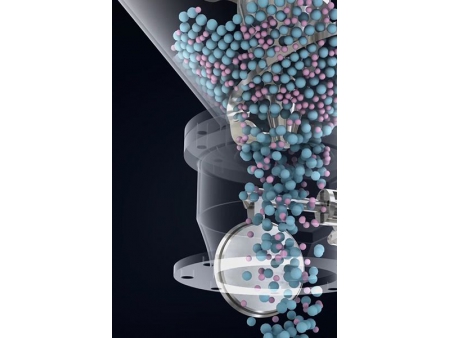
Vertical Ribbon Mixer with CIP
S&L vertical mixers are able to achieve optimal performance for hygienic production by implementing a Clean-in-Place (CIP) system. This feature can be added to all of our models. CIP is an efficient cleaning process that requires some manual preparation steps, such as installing a washing device. Once installed, the system performs a complete cleaning in fully automatic mode through PLC technology. Drying with air is necessary after wet cleaning. With no cross-contamination between batches, you can be assured of the quality of your finished products.
- Two 360-degree rotating spray nozzles are symmetrically arranged on the top of the vessel, forming a 3-meter diameter spherical rotating water curtain under a water pressure of 5 bar. The dual spray nozzles can provide full coverage of the inner surface of the vessel.
- The rotating spray nozzles rotate at a fixed speed, ensuring full coverage of the inner surface of the tank using different atomized fan shapes.
- The spray nozzles are hydraulically driven and do not require external power. They are equipped with ceramic bearings.
- The spray nozzles are designed to be externally mounted through the vessel, facilitating replacement and maintenance.
Vertical Ribbon Mixer with Jacket
The conventional jacket is a popular choice for dryer mixers. It consists of a second shell placed over a portion of the vessel, with cooling or heating medium flowing through the annular space, including internal baffles. As material processing advances, the mixer is increasingly utilized for multi-functional mixing. The dryer mixer can handle materials with a maximum water content of 70% and dry them using a combination of heating jacket and vacuum. In some cases, the drying effect can reduce the water content to as low as 0.05%. The basic design of the dryer is a stationary horizontal cylinder, loaded from the top and discharged from the bottom. The standard mixing tools are plow-shaped and radiate from a horizontal shaft supported by outboard bearings. Other mixing tool designs are also optional.
This dryer operates based on the well-established principle of 'fluidized bed' mixing. It maintains the materials being reacted in a mechanically fluidized suspended state, allowing intimate contact between the reacting mediums (gas-solid or liquid-solid) and the heat transfer surfaces. A heating jacket and vacuum design are essential for this process. During the mixing and drying process, the material is dried by transferring heat from the heating jacket to the vessel. Subsequently, steam pressure builds up inside the vessel, which is then removed by a vacuum pump. Different types of mixers and mixing agitators can be used depending on the specific application. We design our dryer mixers to comply with pressure vessel codes to ensure safety and quality.
S&L powder mixing & blending systems for powders, pastes, slurries, and liquids, are mainly used in the following industries:
- Mixing process systems for the chemical industry
- Mixing process systems for the pharmaceutical industry
- Mixing process for battery industry
- S&L vertical ribbon mixer is equipped with an access door, making it highly convenient for troubleshooting and maintenance.
- This blender be equipped with a CIP system, allowing easy internal cleaning when mixing and blending different materials.
- The vertical mixing equipment can be modified according to different processes to meet your specific needs for mixing and blending.
- The vertical ribbon agitator is used for efficient mixing and blending, providing convenience for cleaning.