Roll-fed J-cut Paper Bag Making Machine with Twisted/ Flat Handles and Top Over-folding
The J-cut paper bag making machine, for bags with twisted or flat handles is a type of innovative machinery, streamlining the production of paper bags with handles folded inside. Starting with paper fed from a reel, the paper bag machine skillfully forms handles and attaches them to the paper. Each step is automated, from handle making and pasting to the precise cutting and folding of the paper sheet. The machine then efficiently applies glue, shapes the bag, and finishes with the bottom folding and gluing, all in one smooth, synchronized process. This fully automated bag making machinery not only enhances efficiency but also significantly cuts down on labor costs, making it an ideal solution for producing quality paper bags.
Model | ZD-FD380QZ | ZD-FD480QZ |
Paper sheet width | 530-1230 mm | 590-1510 mm |
Max. diameter of paper roll | Ø1500 mm | Ø1500 mm |
Inner diameter of paper roll | Ø76 mm | Ø76 mm |
Paper gram | 100-200 g/m² | 100-200 g/m² |
Paper sheet length | 340-640 mm | 420-830 mm |
Finished bag width | 180-380 mm | 200-480 mm |
Paper tube length | 280-580 mm | 360-770 mm |
Bag bottom width | 70-220 mm | 80-260 mm |
Top folding depth | 40-60 mm | 40-60 mm |
Max. production speed | 110 bags/min | 100 bags/min |
Working air pressure | 0.6-0.8 MPa | 0.6-0.8 MPa |
Total power | 380V 3P4L 57kW | 380V 3P4L 57kW |
Weight | 25500 kg | 28500 kg |
Overall dimensions | 17800*4700*3200 mm | 18800*5700*3300 mm |
Twisted rope handle | Q3 | Q4 |
Handle rope height | 90-120 mm | 90-120 mm |
Handle rope diameter | Ø3-6 mm | Ø3-6 mm |
Handle patch length | 152 mm | 190 mm |
Handle patch width | 35-50 mm | 35-50 mm |
Handle rope distance | 76 mm | 95 mm |
Paper patch roll diameter | Ø1200 mm | Ø1200 mm |
Paper patch roll width | 70-100 mm | 70-100 mm |
Paper patch gram | 80-150 g/m² | 80-150 g/m² |
Flat handle | B1 | B2 |
Paper gram for handle | 100-130 g/m² | 100-130 g/m² |
Flat handle width | 12 mm | 15 mm |
Flat handle height | 100 mm | 100 mm |
Flat handle distance | 76 mm | 95 mm |
Diameter of reel paper for handle | Ø1200 mm | Ø1200 mm |
Paper patch gram | 100-150 g/m² | 100-150 g/m² |
Paper patch roll diameter | Ø1200 mm | Ø1200 mm |
Handle patch length | 152 mm | 190 mm |
Handle patch width | 35-50 mm | 35-50 mm |
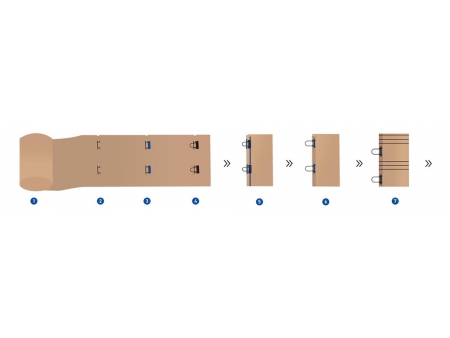
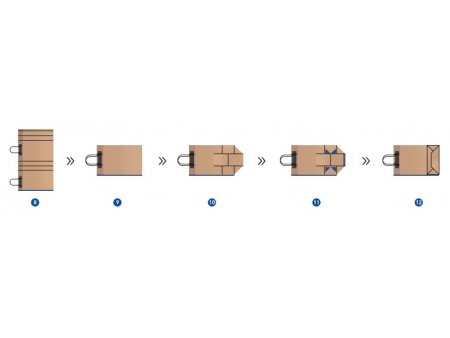
- Paper Roll Feeding
- J Cutting
- Handle Gluing
- Handle Pasting
- Gluing/Paper Cutting
- Top Folding
- Gusset Creasing
- Side Gluing
- Tube Folding
- Bottom Folding
- Bottom Gluing
- Bottom Sealing
- Feeding Unit
The feeding unit is designed for efficiency and ease of use. The roll paper is secured onto an air expanding shaft, then fed into the machine using a swing arm with an advanced hydraulic lifting system. This unit is equipped with an alarm system that activates when paper replenishment is necessary. Furthermore, it incorporates an automatic web guide and uniform tension control, ensuring the paper is fed into the machine with optimal alignment and smoothness. Simplifying the roll change process, a button control allows for easy and quick replacement, enhancing overall productivity that sounds an alarm when paper needs replenishing.
- Handle Making Unit
The handle making unit is designed for effective and accurate handle making. It starts by feeding two rolls of patch paper and one roll of paper rope into the machine. The paper rope is then glued to the patch paper, using both water and hot melt adhesives for a strong bond. After the gluing process, the combined material is compressed to ensure the handles are firmly attached. The final step involves cutting the handles to the correct size and transferring them to the handle patching unit, preparing them for attachment to the bags.
-
- Handle Pasting Unit
The handle pasting unit is designed to paste handles to paper bags with precision and efficiency. After cutting the handles that were made previously, they are accurately placed at the designated position on the paper bag. The unit then applies a water-based adhesive to bond the handle to the bag. Once attached, the handles are firmly pressed onto the bag surface, ensuring a secure hold. This process is completed before the bag enters the pre-creasing stage, preparing it for the final shaping in the forming unit.
-
- Paper Cut and Top Folding Unit
This unit starts by cutting the paper into individual pieces based on the pre-set tube length parameters. Following the cutting, the unit applies glue to the top edge of each paper piece. The final step involves neatly folding over the top edge, ensuring a clean and secure fold. This process is critical for preparing the paper for the next stages of bag assembly.
-
- Bag Forming Unit
In the bag forming unit, the process begins with applying glue along the sides of the paper. This is followed by precise folding to create a paper tube. These tubes are then transferred to the drum mechanism, where they are opened into a four-cornered bottom shape, assisted by a vacuum suction system for accuracy. The final steps involve applying glue to the bottom, sealing it, and shaping the bag into a perfect square form.
-
- Bag Collecting Unit
The bag collecting unit plays a crucial role in the final stages of paper bag production. This unit takes the formed bags, compresses them for consistency, and then outputs the finished bags. An integrated counting system displays the number of bags processed, providing valuable information for quality control and production management.