LD-12B-1850 Automatic Molded Pulp Packaging Machine
Description
LD-12B-1850 automatic molded pulp packaging machine is designed for the purpose of uniting molding and shaping, automated production, energy saving and high yield of pulp molding process of products’ free edge-cutting. LD-12 series molded pulp packaging equipment, which can realize automatic water supply, slurry feeding, slurry mixing, vacuum blank forming, hot pressing drying, shaping and remolding collecting and counting, are energy saving, automatic pulping, and environmental friendly.
Application
The automatic molded pulp packaging machine adopts SIEMENS PLC NC programmable control system in Germany to control each process action, which can be monitored and adjusted on the touchable video screen. The machine can translate plants fiber (sugarcane pulp, bamboo pulp, wheat straw pulp, reed pulp) or wood pulp into food packages such as western-style food, dish, bowl, box, supermarket vegetable tray and various beverage cup, coffee cup and more. The packages are suit for microwave oven, oven, frozen, and distillation. Besides, the package can be used in the fields of industrial and domestic.
- Plate
- Bowl
- Box
- Tray
- Cup
- Slipper
Analysis of production process
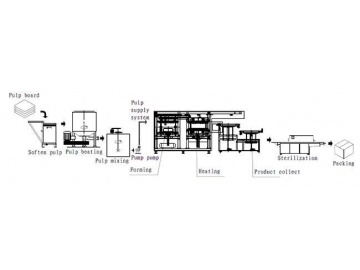
The process can be mainly divided into three steps.
1. First of all, translating pulp board into pulp liquor. The pulp board, after being reduced by hydraulic pulping machine, will come into slurry mixing tank to be mixed with food grade waterproof and anti oil additive before coming into slurry tank. The slurry delivery system will grout accurately and quantitatively, do hydraulic agitation homogenate, vacuum dehydration and molding.
2. Then, molding process. It’s a vital process contains quantitative slurry feeding, back flushing hydraulic homogenization and vacuum adsorption dehydration molding. With advanced technology adoption in forming die, perforation and uneven thickness is reduced during the molding. After molding, the tableware blank is transferred to the hot pressing solidification mold, and then dehydrated, dried and solidified. After that, mechanical hand will remold the collection to finish the process.
3. Finally, finalizing process. With adoption of heat conducting oil-heating device for pulp molding tableware - patent energy saving technology from Far East (ZL 2008 2 0101990.8), it decreases power consumption to 30% and production cost of environmental protection pulp food containers to 70% of original. The process meets the requirement of food packaging hygiene and improves the efficient of energy utilization and the rate of finished products is above 98%. And the product meets the requirements of FDA, SGS, BPI and China's food packaging hygiene requirements.
4. After those three steps, the product will be directly transported to the collecting device for automatic collection and stacking of the products without edge cutting.
Technical ParametersItem | Technical Parameter | Remark |
Exterior size | 9200*2730*3750mm | Manufacturer offer |
Machine weight | 22T | Manufacturer offer |
Worktable size | 1850*1850mm | Manufacturer offer |
Installed capacity | 7.25KW | |
Cycle time | 45s | Calculating with standard 9 inch disk (16g) |
Qualified control range of product weight | ±1.5-2.5gg | Product standard weight (±1.5-2.5g) |
Maximum thermal power of hot pressing die | 260KW | Manufacturer offer |
The height of the product can be produced | ≦100 mm | |
Single day capacity of equipment | 1500 KG (90000) | Calculating with standard 9 inch disk (16g) |
Product quality qualification rate | ≧95%s | In line with the enterprise product appearance inspection standard |
Configuration
Packaging production line of LD-12B-1850 series energy-saving environmental protection equipment is consisted with devices as following: two sets of mold combination machine for automatic pulp molding and shaping, forming slurry pool with overflow device, double vacuum dehydration, spray pressure free edge-cutting device, hot pressing and setting drying hydraulic device connected with hot heat oil, product collection device with manipulator, energy-saving hydraulic device and PLC control system.
The system can realize setting procedures such as product weight and quality control, automatic remolding, collection and counting, time adjustment of drying and heat shaping, power distribution revision, which make it is able to supply water automatically, feed and mix slurry, form vacuum blank, shape under hot pressing and drying, collect and count of mold unloading. As for the automatic collection device for products, it consists optical fiber alarming device and transfer device for monitoring pulp product transferring and other usage. These devices are connected with computer system, if the fault occurs, it will automatically stop the devices and alarm.
Features
1. Semi-automatic pulp molding machine’s parts, such as pipes and valves which contact of the pulp are all made of 304 stainless steel, which is corrosion resistant, heat resistant and good in mechanical properties.
2. The mold of the shaping machine is made of alloy copper or 7075 alloy aluminum with high thermal conductivity, high wear resistance and high strength and high conductivity.
3. What’s more, the machine holds Far East China patents (patent number: ZL201520507523.5): device with one pump, five cylinder and multi position.
4. Specifically, the hot pressing type adopts hydraulic mode, which has high pressure up to 15Mpa and product density with two heating mode: electric or energy saving heat conduction oil heating.
5. Besides, the machine holds the high safety operation rate up to 95% even under 24hours daily.