Plough Shear Mixer
Industrial horizontal mixer for blending powders, granules and pastes
Plough shear mixer, also named ploughshare mixer, plow mixer or plough mixer, is an industrial horizontal mixer specially designed for blending powders, granules and pastes. S&L Ploughshare mixer consists of a cylindrical drum, drive unit, plough shaped mixing elements mounted on a horizontal shaft, and high speed choppers. Plow mixers operate on the principle of a mechanically generated fluid bed with three-dimensional movement of the product. In operation, the shaft rotates at higher speed, mixing tools project and hurl material away from the wall into free space in a crisscross direction, and inversely back again.
The plow separates and lifts the product into three-dimensional motion, while the number and arrangement of the tools insure agitation back and forth along the length of the vessel. When the material flows past the high-speed choppers, it is cut and scattered by the blades, achieving uniform mixing in short time. The choppers help to remove lumps in the raw material, chop pasty additives, and prevent formation of agglomerates on liquid addition.
- Chemical: chemical powders, dye powders
- Cosmetics:
- Battery: battery material
- Pharmaceutical: chemical powders
S&L plough shear mixer is ideal for mixing powders and powders, particles and powders, as well as powders and small amounts of liquid additives.
Pressure/vacuum inside mixer, Jacket for cooling or heating
Model | Total Volume (m³) | Loads Coefficient | Motor Power (kW) | Dimensions (mm) (Max. diameter × height) | Weight (kg) |
0.1 | 0.4-0.6 | 3 | 1270×865×850 | 430 | |
0.3 | 0.4-0.6 | 4 | 2070×1050×1150 | 950 | |
0.5 | 0.4-0.6 | 5.5 | 2180×1200×1300 | 1100 | |
1 | 0.4-0.6 | 11 | 2830×1620×1550 | 1800 | |
2 | 0.4-0.6 | 18.5 | 3420×1810×1758 | 2520 | |
3 | 0.4-0.6 | 18.5 | 3420×2045×1983 | 3200 | |
4 | 0.4-0.6 | 22 | 4200×2140×2123 | 4836 | |
6 | 0.4-0.6 | 30 | 4680×2290×2448 | 8775 | |
8 | 0.4-0.6 | 45 | 5560×2390×2608 | 9360 | |
10 | 0.4-0.6 | 55 | 5140×2390×2850 | 9750 | |
12 | 0.4-0.6 | 55 | 5720×3110×2960 | 10660 | |
15 | 0.4-0.6 | 75 | 5920×3280×3140 | 11050 |
-
-
Drive unit
Standard mixers are driven directly by a gearbox, which provides high torque, reliability, and low noise. Large-scale mixing equipment, on the other hand, utilizes a combination of a gearbox and belt drive to protect the transmission components in case of unexpected situations.
-
-
High speed choppers
The evenly distributed choppers inside the cylinder, when running at high speed, not only disperse the materials axially but also drive the materials to flow along the circumference of the cylindrical body. The central chopper plays an auxiliary mixing role and helps to disperse and disaggregate agglomerated materials.
-
-
Liquid injection
An atomizing nozzle can be added above the choppers to achieve liquid addition and mixing. Due to the lower density of the material at this position under the shearing action of the choppers, the atomized liquid is more easily incorporated into the intermixing with the powder.
-
-
Heating/cooling jacket
Various types of jackets can be added to the outer body of the mixer, allowing for the cooling or heating of the material by injecting cold or hot media into the jackets. Cooling is typically achieved by pumping industrial water into the jackets, while heating can be achieved by introducing steam or thermal oil.
-
-
Discharge valve
Generally a pneumatic flipper valve is adopted. The circular arc valve is tightly embedded in the cylinder, flush with the inner wall of the cylinder, and free from the phenomena of material accumulation and dead corners for mixing. The reliable edge strip-type sealing ensures no leakage during frequent opening and closing.
-
-
Main shaft seal
When mixing ultrafine powders, the use of a new type of balanced seal and packing seal enhances the airtightness and effectively prevent the flow of gas and powder between the inside and outside of the vessel
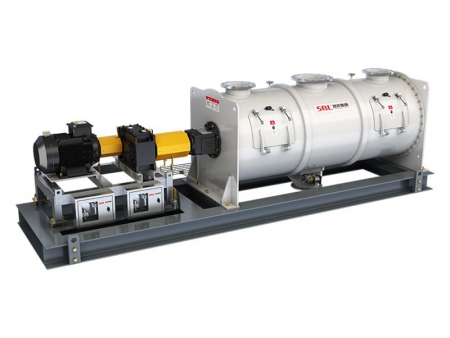
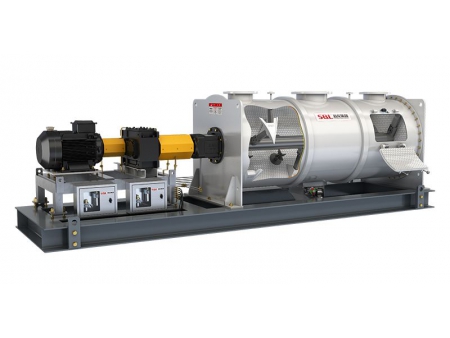
Jacket
After adding a jacket (manufactured according to pressure vessel standards), this plough shear mixer turns into a versatile plow-type mixing and drying machine that combines the processes of reaction, drying, and mixing. It can replace traditional processes in the chemical and other industries, significantly improving product quality and production capacity.
In the mixing process of lithium battery materials such as ternary precursors, the plow-type mixer is an essential choice. The ploughshare mixer consists of a horizontal main shaft, plows or paddle mixer with reasonable static balance distribution as the mixing components. The cylindrical body contains one or more feeding ports, an exhaust port, a central discharge port, etc. The two end faces of the cylinder are fixed by side plates. In the industry, multiple sets of choppers are often used together in the mixing process, and the power drive system is designed separately from the cylinder. With the combined action of the plows and choppers, this mixer creates a centrifugal and convective motion for the powder, achieving thorough mixing in a short time. It is widely used in the lithium battery industry.
- S&L plough shear mixer a high-power blending equipment with high mixing efficiency.
- The super large door makes it easy to maintain the equipment.
- It integrates functions for mixing, drying, and reacting, which can be used as a complete mixing & blending system.
- As a horizontal mixer, it can achieve large mixing output and process large quantities in batches.
- It is a horizontal mixing system that is easy to maintain and has a large output.
- It has three motors, which can achieve high-power operation.
- The two side plows achieve convection mixing, which ensures high-precision and uniform mixing.
- A vacuum feeding machine can be installed on top for automated feeding.
- A dust collector can also be installed on top to reduce smoke and dust emissions and minimize harm to operators.
- For more information on the structure, please consult our technical personnel.
- Continuous blending or batch blending method: Batch processing allows for traceability.
- Batch size: It is important to find the right balance, as an excessively large batch may result in uneven mixing.
- Mixing time: Shorter mixing times lead to lower processing costs and reduced degradation of sensitive materials. However, a balance must be struck between mixing uniformity and cycle time.
- Power consumption: Energy efficiency is crucial. S&L has extensive experience in designing energy-efficient mixing and blending systems.
- Easy discharge: Discharge capability is one of the key functionalities of batch mixers. It is essential to ensure complete discharge of the blended material without any residual.
- Easy cleaning: Proper cleaning is vital to an equipment for mixing and blending different materials. S&L industrial mixers & blenders are integrated with CIP (Clean-in-Place) systems for easy cleaning.
When selecting a mixing & blending system, please inform our technical experts about your requirements. They will provide suitable recommendations to minimize your procurement costs and maximize the equipment efficiency.