Floating Pump Station
Traditional Pump Station
Because of the extremely high cost of investment for traditional pump stations, the government is the primary source of funds.
If the government cannot build these pump stations, the people living in these areas sometimes suffer greatly as a result.
This picture shows the dry land near the Nile river in Sudan.
The disadvantages of traditional pump stations
1. Big buildings and construction projects
2. Large infrastructure requirements
3. Complicated installation
4. Huge capital investment
OUR AIM is to bring water from the river to the people who need it with extremely low cost for Stainless Steel Center Pivot System. The following is our solution for pumping stations which are far easier and cheaper to construct.
The Rainfine Floating Pump Irrigation System includes:
1. Floating pump station
2. FRP pipe production on the farm site
3. Container package booster pump station
4. Pivot irrigation equipment
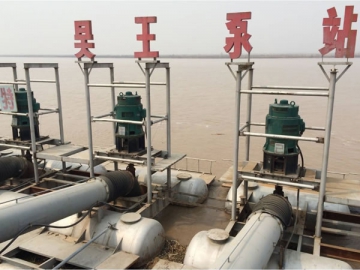
Wu-Wang floating pump station
1. This pump station was built in China in the year 2000
2. The station has 25 2.8m3/s each x 25=70m3/s pumps
3. Charge head is 4m
4. No surveying is needed
5. Less civil works requirements
6. Takes clean water from the top level of the river
7. Easy construction (4 months only)
8. Can be built anywhere along the river
9. Investment costs are much lower compared to traditional pumping systems
The advantage of the floating pump station
1. Can be built in anywhere along the river
2. No surveying necessary
3. Minimal construction requirements
4. Standard factory production
5. Short and easy assembly and commissioning
6. Safe and reliable operation
7. Low maintenance cost
8. Extremely low cost of investment (about 20% of the cost of the traditional pump)
- We need 1400mm x 16km fiberglass reinforced plastic (FRP) pipe to connect the pump station to the reservoir.
- FRP pipe-civil works
Length: 16 km; Diameter: 1400mm; 1.6 Mpa; Friction lose: <1m/km - Total civil works for piping
Width for DN1400 pipe: 2450mm
Civil works for piping per meter:8m³
Civil works for piping 16km: 16000*8=128000m³
- 1. shipment by trucks
- 2. Loading
- 3. Earth open
- 4. Pipe laying
- Excavator: 2 sets
- 16 tons crane: 1 set
- Truck: 3 sets
1. The freight cost of a 40’container from China to Sudan is US$2,300.
2. One container can only load one pipe 12m.
3. The cost for ocean freight is: 16,000m/12m xUS$2,300=US$3,068,200
4. The freight cost of pipe per meter is: US$2,300/12m=US$191.00
5. The inland freight cost from China to the nearest port and from Sudan port to Alrawabi field is very expansive (maybe the same cost as the ocean freight cost).
6. The cost of freight per meter is getting to be very expansive.
If we buy pipe from Egypt or Turkey, the freight cost is slightly less than that in China but still very high.
- Manufacturing equipment: 12 x 40' HC
- Testing equipment: 2x40’HC
Container package booster pump station
Container package booster pump station is the unit with 2×40' containers.
- Each container has 4 pumps all assembled within the factory.
- No need for assembly at the farm site. Only a concrete base is needed to fix the container.
A diesel engine is used to power the pump.
The advantage of the container booster pump station
1. Can be made and assembled within the factory
2. Quality is guaranteed in factory production
3. Low cost of shipment for standard containers
4. Professional technicians are not needed at the working site
5. Low cost of installation and assembling at the site
6. Low maintenance cost
7. Can be moved in the future
- Water canal construction
- Filter system of canal
This wall is engineered to block sediment in the overflow channel.
- Walking canal for dredging equipment beside the ditch. Dredging should be performed regularly once a year.
- The spillway between the main canal and grit chamber can block sediment from flowing into the reservoir.
- HDPE geo-membrane is installed in the bottom of the dam to protect water leakage and protect the side of the water canal
- If we build the pump pipeline in the low position
- we can build pump station here.
- Total length: 5.51km Elevation (High): 393m Elevation (Low): 363m The difference from high to river is 30 meters.
- This is the main pipe which is 5.51km for the first section 31 pivot.
- The second part of the main pipe is 3.16km Elevation (High): 413m Elevation (Low): 393m. The difference from the high point to the river is 20 meters.
- This is the first phase 32 pivots.
- This is the second phase 32 pivots.
Proposal for the project
1.We will build a floating pump station similar to the Wu-Wang pump station.
2. The total flow rate of the station for 64 pivots should be 12,800m3/hr (3.47m3/s).
3. The first phase charge head is 40m with flow 6,400m/3/hr(1.78m3/s) for 32 pivot and the second phase charge head is 30m with 6,400m3/hr(1.78m3/s) for 32 pivot.
4. The total power consumption of the two stages is about 3.9 MW.
5. Each container booster pump can supply water for 8 pivots. 8 container booster pump stations are needed for 64 pivots.
Cost calculation of Alrawabi
Cost for equipment
1. Main pump station: US$1,000,000 Pump: 3×1.78m3/s 40m head Motor: 3x 700kw /10kv floating system
2. Booster pump station: US$900,000 Pump: 3x 1.78m3/s 30m head Motor: 3x600kw/10kv Pump house
3. Container pump: US$900,000 200m3/hr x 8 pumps x 8 units = 12,800 m3/hr(3.6m3/s)
4. FRP pipe equipment and the shipment: US$300,000
5. Pipe 8.67km: US$420.00/m x 8.67km=US$3,641,400 FRP pipe 0.6Mpa: 1,400mmx20.5mm, 186kg/m
Grand total: US$6,740,000
Note: The cost of the canal and the dam is not included in the above calculation.
The electrical cost for water per cubic meter
If we use this system, the total power required is :
Main pump station: 3x700kw=2,100kw
The booster station:3x600kw=1,800kw
The total power required: 2,100kw 1,800kw=3,900kw
The fee for electric power in Sudan is 0.20SDG/kwh
The power cost per hour is: 3,900kw x 0.20SDG/kwh=780.00SDG
The water charged per hour: 2.10m3/s x 3 pumps x 3600s=21,600 m3
So the cost for water per cubic meter is: 780SDG/ 21,800m3=0.036 SDG/m3 (US$0.0045/m3)
This is much cheaper than using a diesel powered system diesel.
The equipment cost for water per cubic meter
1. The total investment for the equipment is US$6,740,000 :
If this system can be use for 6 years, the investment per year should be: US$6,740,000 /6=US$1,123,333
2. The water pumped from river per year: 1.78m3/s x 3pumps x 3600 s x 24 hr x 300days=138,412,800m3
3. The investment cost of water per cubic meter US$1,123,333 / 138,412,800m3=US$0.008/m3
The total cost of electric and equipment
The total cost ( investment cost electric power) US$0.008 x 8 0.036 SDG= 0.10 SDG/ m3
The percentage of water cost in alfalfa production
If 1000m3 water can produce 1 ton of alfalfa.
The cost for water in 1 ton alfalfa is: 0.10SDG x 1000=100.00SDG
The rate from US$ to SDG is 1:8
The cost of water in 1 ton alfalfa is 100SDG/ 8= US$12.50
If the price of alfalfa is US$320.00/ton
The cost of water in 1 ton alfalfa is: US$12.5/320=4%
We can calculate for cost of water from bore holes produced using diesel engine power
Cost calculation of bore well system with diesel engineThis is the pivot system with the water supply from bore wells powered by diesel engine.
The diesel cost for water per cubic meter:
1. The diesel engine for 50ha pivot is 140kw, The diesel consumption is 36L/h
2. The cost of diesel in Sudan is US$0.60/L
3. The cost of diesel per hour: 36L/h x US$0.60=US$21.00
4. The water quantity from bore hole is 200m3/h
5. The cost of water per m3 is: US$21.00/200m3=US$0.11
6. Electric power cost is US$0.0045/m3 which is 4% of the diesel cost
Equipment cost for water per cubic meter
1. The investment cost for diesel engine and bore hole is US$180,000 /pivot
2. If we use it for 6 years, the investment each year is: US$180,000/6=US$30,000
3. The water pumped from bore hole per year is 200m3/h x 24 hr x 300 days=1,440,000m3
4. The cost of investment of water per cubic meter: US$30,000/1,440,000=US$0.028 /m3
5. The floating system cost is US$0.008/m3 which is 28% of the bore hole system
The total cost of diesel and equipment
1. Total cost of water: US$0.028 US$0.11=US$0.138 /m3
2. Of 1000 tons of water can produce 1 ton of alfalfa, the cost of water per ton of alfalfa is: US$0.138 /m3 x1000=US$138.00.
The percentage of water cost in one ton alfalfa
If the price of alfalfa is US$320.00/ton.
The cost of water in 1 ton alfalfa by bore hole is: US$138/320=43%
For the floating system, this number is 4%.
Summary
The key points of the project are:
1). The floating pump can save an enormous amount of money for the cost of construction
2). FRG pipe produced on site can save money by avoiding large shipping costs
3). The container package booster pump can prevent the cost of installing civil works and they are easier to assemble
4). The cost of water is extremely low for crop production
5). The cost of water from bore hole run by diesel is 43% of the alfalfa sales value
6). The cost of water from floating pump station is only 4% of the alfalfa sales value
7). This will bring great agricultural opportunities to impoverished areas of Africa