ASME Pressure Vessel, Heat Exchanger and Rotary Dryer
Our company is committed to R&D, design and manufacture of various ASME pressure vessels, high pressure heat exchangers and rotary dryers. We have obtained design and manufacturing licenses for ASME pressure vessels, ISO9001 quality management system certification and French Bureau Veritas certification. In our production process, we make use of different kinds of digital flexible manufacturing techniques such as CAD, CAM and CAPP. In addition, we introduce state-of-art production equipment and recruit skillful and experienced technicians. As a result, we are able to fully satisfy our customers with our Chemsta-branded devices. Up to now, we have successfully sold about 10,000 superior quality pressure vessels to many countries, which include America, Canada, Russia, Indonesia, Vietnam, Kazakhstan and Pakistan.
We are able to produce various pressure vessels based on customers’ requirements. Our products are listed as followed.
Rotary Tube Bundle Dryer
Features
Compact layout, simple structure, high heat change efficiency, low heat consumption, energy conservation, a wide range of applications, large capacity, large evaporation capacity, thorough blending of material in the rotary drum, no residue
Applications
The dryer is extensively applied to dry loose materials in chemical industry, light industry and food industry, grain industry and fodder industry.
Heat Source
Low or medium pressure steam
Rotary Dryer with Large Drum
Features
1. The dryer features low working temperature and high safety factor because it is able to efficiently prevent combustion of materials dried.
2. Combination of hot wind and steam contributes to large evaporation capacity.
3. Hot wind, inclined drum and big spiral installed inside of the drum together make the materials flow flexibly in the drum.
Applications
1. The dryer is suitable for drying of biofuels such as fibrous barks, saw powder, bamboo chippings, wooden chippings, wood shavings, barley straws, oat straws, wheat straws, rye straws, straws, sorghum straws, maize straws, bean stalks, animal waste.
2. In chemical industry, mining industry and metallurgical industry, our dryer can be used to dry large particles including mill tailings, blast furnace slags, coals, metal powder and phosphatic fertilizers, etc.
3. It is also applied for drying of stillage, embryos, starches, soybeans, bean dregs in grain industry.
Heat Source
Hot wind/flue gas/low or medium pressure steam
Horizontal Disc Dryer
Features
Indirect drying, small oxygen concentration, small amount of exhaust gas, large evaporation area, small occupied area, low rotating speed, minimum wear and breakage
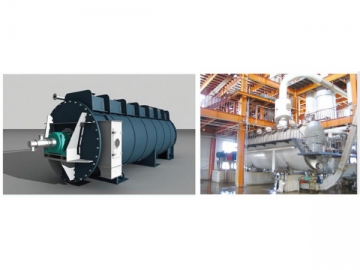
Applications
Environmental Protection Industry: drying of sludge(moisture content <85%)
Food Industry: drying of plant protein powder, animal protein powder
Heat Source
Low or medium pressure steam/ conduction oil
Device Name: Combustible Gas Heater | Medium: water vapor/natural gas | ||||
Design Pressure (MPa) | Design Temperature (℃) | Thermal Treatment Method | Nondestructive Testing Method | ||
18.3/4.48 | 55/288 | PWHT | 100%RT/HLT | ||
Texture | SA516Gr.70N/SA179/SA105/SA106B | Dimensions: Φ508*9,000*50 | |||
Heater Introduction | Complied with ASME standards,the heater is designed to heat natural gas using water vapor. Then the natural gas can enter sequential combustor directly. |
Device Name: Evaporator | Medium: water vapor/mixed oil | ||||
Design Pressure (MPa) | Design Temperature (℃) | Thermal Treatment Method | Nondestructive Testing Method | ||
0.65/-0.1 | 168/130 | / | 20%RT | ||
Texture | SA240 Gr.304/SA312 TP304 | Dimensions: Φ900*5,000*10 | |||
Evaporator Introduction | Complied with ASME standards,the heater is designed to heat mixed oils using water vapor. Its tube is filled with mixed oil, while its shell is filled with water vapor. Solvent in the mixed oil will vaporize on heating and then be recycled for subsequent sections. |
Device Name: Three-Phase Horizontal Separator | Medium: acid medium | ||||
Design Pressure (MPa) | Design Temperature (℃) | Thermal Treatment Method | Nondestructive Testing Method | ||
10 | -0.489361702 | PWHT | 100%RT | ||
Texture | SA516 Gr.70N/SA350/SA333 Gr.6 | Dimensions: Φ1,800*8,200*20/Φ1,400*6,000*60 (6 sets in total) | |||
Separator Introduction | Complied with ASME standards and America NACE MR0175 standards, the separator is mainly applied in oil fields for separation of water-oil-gas three phase liquids. It is able to efficiently prevent stress cracking, hydrogen induced cracking, stepwise cracking of sulfides. The minimum design temperature of the metal used for production of the separator is -46℃. Design pressure is 10MPa. We are the first one to make this kind of separator in China. |
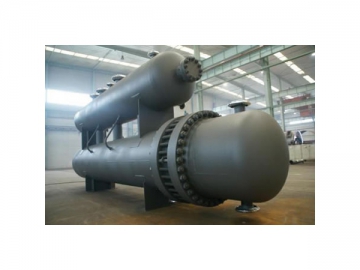
Vessel Name: Filter | Medium: lubricating oil | ||||
Design Pressure (MPa) | Design Temperature (℃) | Thermal Treatment Method | Nondestructive Testing Method | ||
1 | 125 | / | 100%RT | ||
Texture | SS304 | Dimensions: Φ900*1,200*10/Φ1,000*1,300*10 | |||
Vessel Introduction | Complied with ASME standards, the filter is designed to filter lubricating oils. |
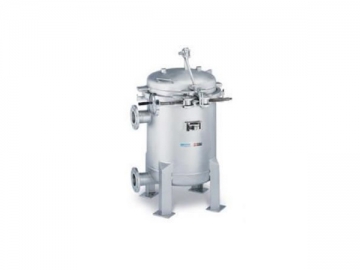
Vessel Name: Vapor Generator | Medium: water vapor/conduction oil | ||||
Design Pressure (MPa) | Design Temperature (℃) | Thermal Treatment Method | Nondestructive Testing Method | ||
6.6/0.66 | 305/345 | PWHT | 100%RT | ||
Texture | SA516 Gr.70N/SA 105/SA 106B | Dimensions: Φ900*5000*30/Φ800*4,000*30 | |||
Vessel Introduction | Our vapor generator is designed in accordance with ASME standards. Its tube is filled with conduction oil, while the shell is filled with water and water vapor. In this way, the water in the shell will be converted into steam by heat of conduction oil. Then, the steam obtained will be used for sequential industrial production. |
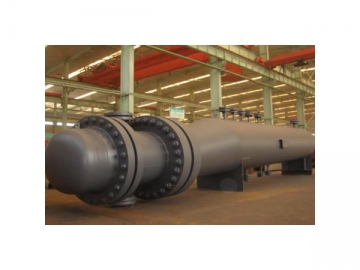
Vessel Name: Vapor Generator | Medium: water vapor/conduction oil | ||||
Design Pressure (MPa) | Design Temperature (℃) | Thermal Treatment Method | Nondestructive Testing Method | ||
6.5/0.4 | 282/300 | PWHT | 100%RT/UT | ||
Texture | SA516 Gr.70N/SA 105/SA 106B | Dimensions: Φ900*5,000*30/Φ800*4,000*30 | |||
Vessel Introduction | Our vapor generator is designed in accordance with ASME standards. Its tube is filled with conduction oil, while the shell is filled with water and water vapor. In this way, the water in the shell will be converted into steam by heat of conduction oil. Then, the steam obtained will be used for sequential industrial production. |
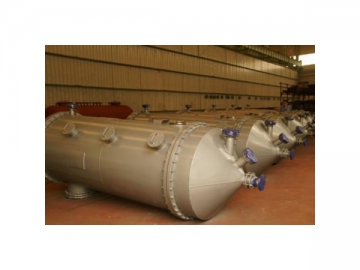
Vessel Name: Condenser | Medium: water/vapor | ||||
Design Pressure (MPa) | Design Temperature (℃) | Thermal Treatment Method | Nondestructive Testing Method | ||
Constant Pressure | Room Temperature | / | / | ||
Texture | S30408/Q235B/20# | Dimensions: Φ1,800*8,200*20/Φ1,400*6,000*60 | |||
Vessel Introduction | Our condenser is designed for solvent condensing section in oil plants.The tube and the shell are filled respectively with water and solvent containing vapor, which will be cooled into liquid and then recycled for subsequent sections. |
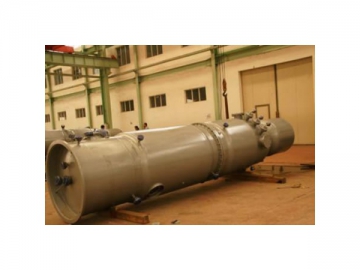
Vessel Name: Stripping Tower | Medium: water vapor/mixed oil | ||||
Design Pressure (MPa) | Design Temperature (℃) | Thermal Treatment Method | Nondestructive Testing Method | ||
0.35/0.15/0.035 | 160/130/100 | / | 20% RT | ||
Texture | Q245R/Q235B/20# | Dimensions: Φ1,300*700*8 | |||
Vessel Introduction | Our stripping tower is designed for solvent distillation section in oil plants. It is able to separate solvent with relatively higher concentration from mixed oils as much as possible. The solvent will be recycled for subsequent sections. |