Energy Saving Plastic Auxiliary Equipment PET Crystallizer
Application
The energy saving plastic auxiliary equipment PET crystallizer is carefully engineered for processing crystallized amorphous phase materials, PET raw materials, and for the recycling of materials that have not been crystallized and can be dried directly at high temperatures. The crystallized materials can be mixed with new PET materials in certain proportions and then they can be dehumidified and dried together. This significantly lowers production costs and it is widely applied in PET sheet production operations.
Output | Model | Air blower | Heating power | Reduction gear |
300kg/h | C1200L | 3KW | 27KW | 2.2KW helical gear |
400kg/h | C1600L | 4KW | 30KW | 2.2KW helical gear |
500kg/h | C1800L | 5.5KW | 36KW | 2.2KW helical gear |
600kg/h | C2000L | 7.5KW | 42KW | 2.2KW helical gear |
700kg/h | C2300L | 11KW | 43KW | 6KW |
800kg/h | C2500L | 11KW | 45KW | 7.5KW |
Workshop crystallization debug site
Features
1. The crystallizer stirs at a fixed speed to prevent bonding throughout the whole process.
2. The whole process lasts 30 minutes, with high efficiency and energy saving operation.
3. The inner wall uses stainless steel 304 mirror surface treatment.
4. The cyclone dust collector is equipped to effectively reduce the load of the return air filter and prolong the service life of the equipment, as well as reduce cleaning times.
5. Complete safety measures with a circle ladder stand.
Main components
- Cyclone filter dust collector
- Crystallizing stirring hopper
- Feeder
- Material collector
1. 80mm thick insulation layer observation door, convenient for observation.
2. Wrapped with 80mm aluminum silicate cotton to lock in heat and save energy.
3. Anti-eccentric blanking device, uniform blanking, no material fault and single side blanking
4. Installed with ladder and fence, safe for workers to install and maintain.
5. The one touch pneumatic cyclone filter dust collector is simple and easy to maintain, reducing the incidence of scald and other accidents
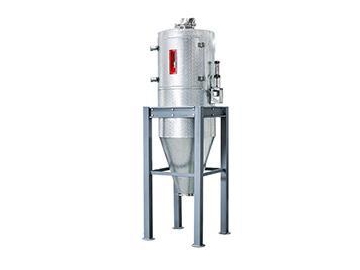
1. The cyclone dust collector effectively reduces the load of the return air filter and prolongs the service life of the equipment.
2. Stainless steel inside, equipped with independent observation window and 50mm thick asbestos insulation layer, can effectively prevent heat loss
3. The cylinder controlled built-in filter core is safe and convenient for disassembly.
4. Excellent dust isolation effect that well guarantees the cleanliness of the material and the dust is easy to be cleaned.
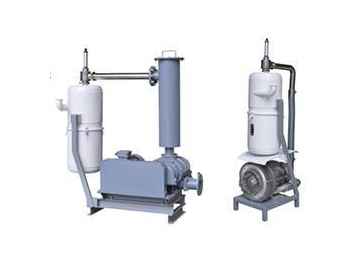
The HF feeder series is equipped with a high efficiency vacuum pump with a delivery capacity of up to 1200 kg/h, the maximum conveying distance of 100 meters. It is configured with a cylinder filter which is tightly structured and combines the cyclone effect with dust separation, and is especially suitable for the delivery of dust laden materials
Features
1. Maintenance free motor, convenient filter core cleaning.
2. Noise level is lower than 78DB (A)
3. Vertical design scheme, small covering area.
What is the working principle of the PET crystallizer?
Amorphous PET bonds at high temperatures and the main purpose of crystallization is to prevent PET materials from doing this. Common methods are to stir or use airflow to boil the PET while drying. The temperature continues to rise and when reaching 160℃, spherical crystals are produced.
The maximum crystallization degree of PET is about 55%, the crystallization temperature range is 120~220℃, and the crystallization time is 1~2 hours. The higher the drying temperature, the higher the drying rate; the shorter the drying time, the lower the moisture content of the raw material.
The drying temperature of the stirred type crystallizer is usually between 120~160℃. The dehumidification drying temperature is between 160~180℃. The PET is boiled with airflow while drying. The higher the drying wind speed, the higher the relative speed of PET and airflow will be, so that the drying time will be shortened, but the dust produced by the system will also increase correspondingly, thus the excessive dust must be removed. The lower the moisture content (dew point) of hot wind, the faster the drying rate of raw materials, and the lower the balanced moisture of the corresponding raw materials.
Considering the processing cost and energy consumption, during the actual processing cycle, for preforms or injection molding, the dew point value less than -50℃ can meet the drying requirement that the moisture content of raw material is less than 50ppm. For extrusion molding, the dew point value less than -40℃ can meet the drying requirement that the moisture content of raw material is below 100ppm.