High-Speed Acid-Free Hot-Dip Galvanizing/Galfan Steel Wire Production Line
Since 2002, Gongda has been engaged in the research and development of Galfan hot-dip coating processes and equipment. In 2005, we built China’s first independently developed single-coating Galfan steel wire production line. In 2009, we launched the country’s first low-carbon steel wire reduction-process Galfan production line. By 2012, we successfully implemented China’s first fully acid-free Galfan galvanizing line, and in 2014, we applied the acid-free process to bridge cable Galfan coating production lines.
- Environmental compliance: Ultrasonic water cleaning replaces traditional hydrochloric acid pickling, meeting environmental protection standards and resolving challenges related to acid recovery and discharge. This also reduces waste acid treatment costs.
- High efficiency: The high-speed galvanizing line is designed for DV values ranging from 120 to 180 mm·m/min. A single steel wire production line can deliver the same capacity as three conventional galvanizing lines, significantly reducing equipment investment and production costs.
- Product types: High-carbon steel wire, hot-dip galvanized / Galfan / zinc–10% aluminum coatings
- Diameter range: 0.8–1.6 mm, 1.6–4.0 mm, 4.0–8.0 mm
- Coating thickness: 40–450 g/m²
- Number of wires: 6–40 wires
- DV value: 120–180 mm·m/min
- Annual output: 10,000–30,000 tons
Hot-Dip Galvanizing Process
Pay-off (spool type) → Straightening → Electrolytic alkaline cleaning → Water rinsing → Ultrasonic cleaning → Water rinsing → Fluxing → Drying → Hot-dip galvanizing (electricity/natural gas/LPG) → Wiping (gas wiping/block wiping) → Cooling (air/water) → Post-treatment (passivation/waxing) → Take-up (inverted type star-shaped type/ spool type)
Hot-Dip Galfan or Zinc-10% Aluminum Process:
Pay-off (spool type) → Straightening → Ultrasonic cleaning → Water rinsing → Electrolytic alkaline cleaning → Water rinsing → Fluxing → Drying → Hot-dip galvanizing (electricity/natural gas/LPG) → Wiping (gas wiping / inclined lift wiping / block wiping) → Galfan fluxing → Galfan drying → Hot-dip Galfan coating (electricity/natural gas/LPG) → Wiping (gas wiping/block wiping) → Cooling (air/water) → Post-treatment (passivation/waxing) → Take-up (spool type)
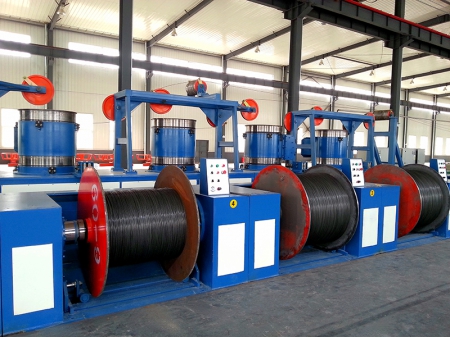
Pay-off Unit
Given the stringent requirements for wire stability in high-speed galvanizing lines, we recommend using an active-drive spool pay-off unit. This pay-off system forms a synchronized tension control loop with the take-up equipment to ensure consistent and stable wire tension throughout the entire process.
Electrolytic alkaline cleaning
To meet the demands of high-speed hot-dip galvanizing lines for steel wire, degreasing of the wire surface is carried out using an electrolytic alkaline cleaning process. Our electrolytic cleaning system features three-sided electrode plates, delivering cleaning performance up to three times higher than conventional electrolytic degreasing and five times more effective than standard hot alkaline cleaning. For convenient daily operation, the electrolytic alkaline cleaning system includes an external circulation tank that supplies cleaning solution to the electrolytic bath, allowing for easy heating, replacement, and maintenance of the cleaning fluid.
Electrolytic alkaline cleaning tank
Filter press for electrolytic cleaning bath
Electrolytic alkaline solution storage tank
Ultrasonic cleaning
Ultrasonic cleaning is necessary for achieving acid-free galvanizing. Unlike conventional systems that rely on mild acids like oxalic or acetic acid, our equipment is designed to meet process requirements using only water. This approach simplifies operation, avoids chemical handling, and still delivers the necessary cleaning performance for the production line.
Ultrasonic cleaning tank
Ultrasonic cleaning solution tank
Ultrasonic generator
Hot-dip galvanizing
The ceramic galvanizing kettle is one of our patented solutions, designed to meet demanding production needs with flexibility and reliability. We provide two heating options: internal heating, which has been consistently used in industrial applications for nearly 20 years, and overhead heating. With the overhead heating system, we’ve improved traditional burner designs by adding a precise combustion control unit that regulates the air-fuel ratio. This adjustment significantly cuts down the buildup of zinc dross in the combustion chamber. Additionally, the setup includes a heat recovery system that captures excess heat and transfers it to the drying oven through a heat exchanger. By reusing this energy, the process becomes more efficient overall and helps reduce production costs.
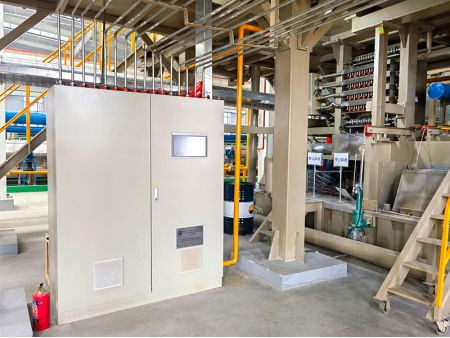
For high-speed hot-dip galvanizing lines, our wiping system uses gas wiping to control the zinc layer thickness precisely by regulating pressure, flow, and temperature. This approach keeps the coating within a tolerance of ±10 g/m². When thinner coatings are needed, typically between 40 and 120 g/m², the system integrates straight-lift and inclined-lift asbestos block wiping devices, which help maintain uniform results. The wiping system is designed to let operators easily switch between three modes, straight gas wiping, straight-lift block wiping, and inclined-lift block wiping, depending on specific production requirements.
Auxiliary Equipment
Titanium flux tank
Dual zinc-aluminum galvanizing furnace
- Post-galvanizing wire cooling system
- Galvanizing measurement sensor
- Large heavy-duty spool take-up machine
- Production line control cabinet