Direct Steam Retort
Direct Steam Retort
Direct steam retort is the simplest and most dependable type of autoclave that provides a proven method for tin can sterilization. During the sterilization, the air is evacuated from the retort by flooding the vessel with steam, exhausting air through the vent valve. There is no overpressure during the sterilization phases, because air is not permitted to enter the vessel at any time during the sterilization step. But there may be air overpressure applied during the cooling steps to prevent container deformation.
In compliance with the requirements of FDA/USDA, the direct steam retort is optimized for automation and energy saving. Our steam retort has been widely used in canned food factories and is still favored by many customers.
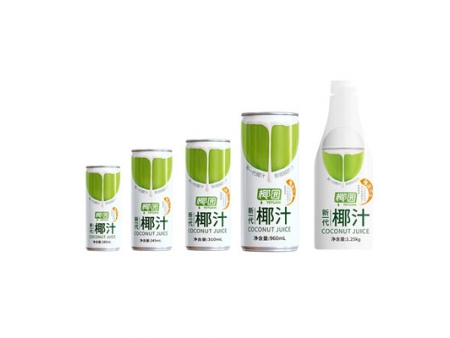
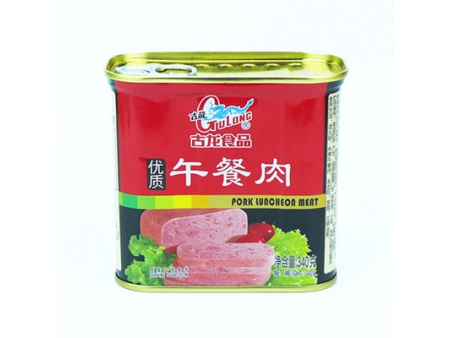
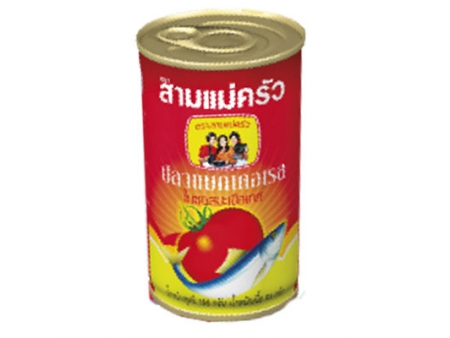
- Package type: rigid containers such as cans
- Food type: beverages (protein powder, tea, coffee), fruits and vegetables (mushroom, beans), meats, fish and seafood, baby food, ready meals and soups, porridge, pet foods
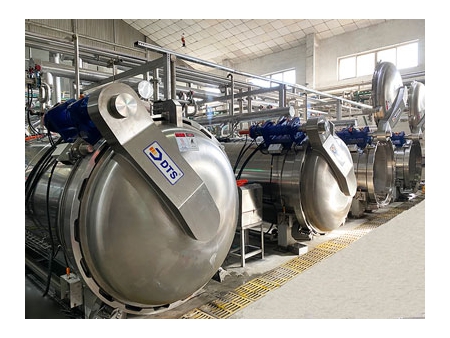
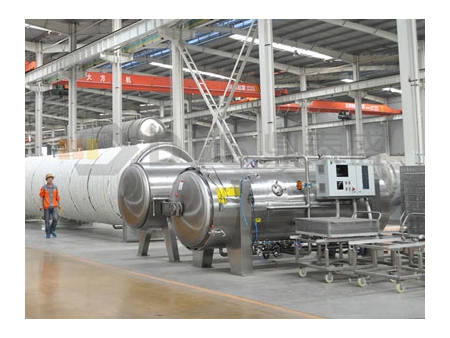
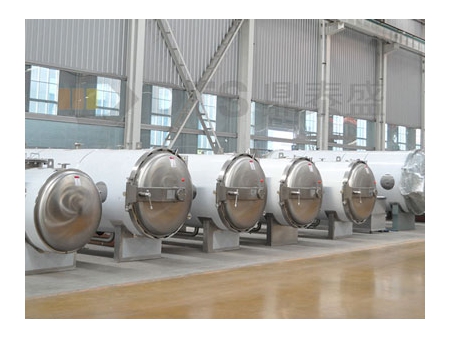

- Uniform heat distribution
- In direct steam retort, the air is exhausted from the vessel and saturated steam is applied for sterilization. Therefore, the temperature inside the vessel is uniform in the end of come-up vent phase.
- Ease of operation, reliability
- Compared with other sterilization methods, steam sterilization process uses steam as the only heating media during the heating and sterilization processes. So the only thing that needs to be managed is the steam to keep the batch of products consistent.
- In compliance with FDA/USDA certificate
- Backed by its team of seasoned thermal processing specialists, DTS has become a member of IFTPS and works in full cooperation with FDA-recognized third-party accreditation bodies. Years of experience in working with many North American customers means we understand the regulatory requirements of FDA/USDA and state-of-the-art sterilization technology.
(the above sizes can support 2 to 6 baskets)
First, send product into the sterilization retort in a basket and then close the door, which is secured by a triple safety interlock. The whole sterilization process is then automated and controlled by PLC.
Next, steam is introduced into the chamber through a diffusion pipe inside the retort while air is expelled through an exhaust port. Once the pre-set time and temperature for exhaust are achieved, the heating phase commences. It’s crucial to maintain saturated steam in the chamber throughout the heating and sterilization process, without any residual air to prevent uneven heat distribution, leading to incomplete sterilization. The vent outlet remains open during the entire process, ensuring convection currents to maintain uniform temperature.
The cooling phase occurs in two stages, mild cooling and full cooling. The former helps to prevent pressure loss within the retort and ensures that product packaging remains intact without getting distorted.
Because saturated steam is used for sterilization, the pressure in the sterilization retort corresponds exactly to the saturation pressure of the steam and is only suitable for rigid containers with a wide range of pressure requirements, such as iron cans.
The temperature distribution inside the retort has a uniformity of /- 0.5℃.