Self-Drilling Anchor Bolts for Ground Support
The self-drilling anchor bolt is manufactured using thick-walled seamless steel pipes that meet API standards. These pipes undergo a warm thread rolling process to create precise threads, which are available in R-thread (Round), compliant with ISO standards, or T-thread (Trapezoidal), tailored to company specifications.
The process of making the threads not only ensures that they are accurate, but it also refines the steel's grain structure, making the anchor bar stronger. To protect the anchor bar from environmental damage and corrosion caused by soil and rock, the surface can be treated with hot-dip galvanization or an epoxy coating, ensuring long-lasting durability and performance.
The self-drilling anchor system is a tool that features a hollow threaded anchor bar paired with a compatible drill bit, enabling drilling, anchoring, and grouting to be completed in a single step. This system is primarily used in engineering applications such as slope stabilization, tunnel pre-support, and micropile reinforcement. It is widely adopted across industries, including mining, tunneling, railways, and subways, due to its efficiency and versatility.
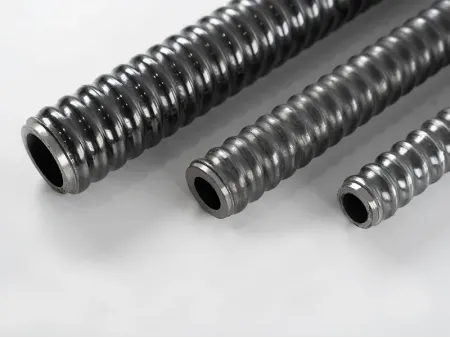
Size | Outer Diameter (mm) | Inner Diameter (mm) | Cross Sectional Area (mm²) | Ultimate Load (kN) | Yield Load (kN) | Agt (%) | Weight (kg/meter) | |
R25N-14 | 25.0 | 14.0 | 290 | 200 | 150 | >10% | 2.30 | |
R32L-22 | 32.0 | 22.0 | 350 | 210 | 160 | >10% | 2.80 | |
R32N-21 | 32.0 | 21.0 | 370 | 280 | 230 | >6% | 2.90 | |
R32N-18.5 | 32.0 | 18.5 | 430 | 280 | 230 | >10% | 3.40 | |
R32S-17.5 | 32.0 | 17.5 | 440 | 360 | 280 | >6% | 3.50 | |
R32S-15 | 32.0 | 15.0 | 520 | 360 | 280 | >10% | 4.10 | |
R32SS-14 | 32.0 | 14.0 | 520 | 405 | 350 | >10% | 4.10 | |
R38N-21 | 38.0 | 21.0 | 620 | 500 | 400 | >6% | 4.90 | |
R38N-19 | 38.0 | 19.0 | 700 | 500 | 400 | >10% | 5.50 | |
R38S-18 | 38.0 | 18.0 | 700 | 560 | 460 | >10% | 5.50 | |
R51L-38 | 51.0 | 38.0 | 760 | 550 | 450 | >6% | 6.00 | |
R51L-36 | 51.0 | 36.0 | 970 | 550 | 450 | >10% | 7.60 | |
R51N-36 | 51.0 | 36.0 | 970 | 800 | 630 | >6% | 7.60 | |
R51N-33 | 51.0 | 33.0 | 1070 | 800 | 630 | >10% | 8.40 | |
R51S-30 | 51.0 | 30.0 | 1160 | 930 | 730 | >10% | 9.10 | |
T76N-49 | 76.0 | 49.0 | 2100 | 1600 | 1200 | >6% | 16.5 | |
T76S-45 | 76.0 | 45.0 | 2420 | 1900 | 1500 | >6% | 19.0 | |
T30-11 | 30.0 | 11.0 | 420 | 320 | 260 | >10% | 3.30 | |
T30-14 | 30.0 | 14.0 | 370 | 275 | 220 | >10% | 2.90 | |
T30-16 | 30.0 | 16.0 | 340 | 245 | 190 | >10% | 2.70 | |
T40-16 | 40.0 | 16.0 | 900 | 660 | 525 | >10% | 7.10 | |
T40-20 | 40.0 | 20.0 | 710 | 540 | 425 | >10% | 5.60 | |
T52-26 | 52.0 | 26.0 | 1270 | 930 | 730 | >10% | 10.0 | |
T73-56 | 73.0 | 56.0 | 1380 | 1035 | 830 | >6% | 10.8 | |
T73-53 | 73.0 | 53.0 | 1780 | 1160 | 970 | >6% | 14.0 | |
T73-45 | 73.0 | 45.0 | 2230 | 1600 | 1270 | >6% | 17.5 | |
T73-35 | 73.0 | 35.0 | 2700 | 1865 | 1430 | >6% | 21.2 | |
T103-78 | 103.0 | 78.0 | 3180 | 2270 | 1800 | >6% | 25.0 | |
T103-51 | 103.0 | 51.0 | 5600 | 3660 | 2670 | >6% | 44.0 | |
Thread direction | Left hand / Right hand | |||||||
Thread standard | ISO 10208 / ISO1720 / Other international standards |
To reduce corrosion and extend the service life of anchor systems, Sinodrills offers a hot-dip galvanization option. This process provides enhanced durability and protection against environmental factors. A complete hot-dip galvanized system typically includes the following components:
All hot-dip galvanized products are manufactured in strict compliance with the following standards, ensuring consistent quality and performance:
For permanent projects, particularly underground constructions, a duplex-coated system is essential. This innovative system integrates two layers of corrosion protection: hot-dip galvanization and an epoxy coating. This dual-layer approach offers superior durability and resistance against environmental and chemical degradation.
The duplex-coated system is engineered to meet the stringent requirements of permanent engineering projects and complies with the following standards:
- 01Construction Process
The self-drilling anchor bar combines drilling, grouting, and anchoring into a single, seamless process. Grouting occurs simultaneously with drilling, which simplifies the installation. In contrast, conventional anchor bars require multiple steps: first drilling the hole, then inserting the anchor bar, and finally grouting. This makes the process lengthier and more labor-intensive for conventional systems.
- 02Geotechnical Suitability
Self-drilling anchor bars excel in complex geological conditions, such as fractured rock, weak soil, and flowing sand. They can adapt to these challenging environments without compromising performance. On the other hand, conventional anchor bars often encounter issues such as borehole collapse or difficulty forming stable holes, which can lead to delays and reduced reliability in such conditions.
- 03Borehole Quality
With self-drilling anchor bars, grouting is performed during the drilling process, ensuring that voids in the borehole wall are effectively filled. This results in superior borehole quality and enhanced stability. For conventional anchor bars, grouting is done after drilling, which may result in less stable borehole walls and inconsistent filling, potentially compromising the system's integrity.
- 04Construction Efficiency
The integrated construction method of self-drilling anchor bars eliminates unnecessary steps, significantly improving efficiency and reducing construction time. Conventional anchor bars, by contrast, require a more cumbersome multi-step process that is less efficient and more time-consuming.
- 05Anchoring Effectivenes
Self-drilling anchor bars provide timely and uniform grouting, which creates stronger bonding with surrounding soil and rock, delivering superior anchoring performance. Conventional anchor bars, however, may experience inconsistent anchoring effectiveness due to factors such as borehole quality and grouting methods, which can make their performance less predictable.
- 06Anchor Bar Structure
Self-drilling anchor bars feature a hollow structure, making grouting more efficient and precise. Conventional anchor bars, being solid, lack this advantage. For example, in a tunnel project with complex geological conditions, conventional anchor bars may face difficulties with drilling and grouting, slowing down progress and compromising anchoring. By comparison, self-drilling anchor bars facilitate faster borehole formation and superior anchoring performance, ensuring project success even in challenging conditions.