Die-cut Handles Block Bottom Bag Making Machine
This bag machine is used to make paper bag with die-cut handles, which is ideal for the production of various paper bag types, including recycled paper bags, food paper bags, shopping paper bags, etc. It uses blank or printed roll paper to create paper bags of various sizes.
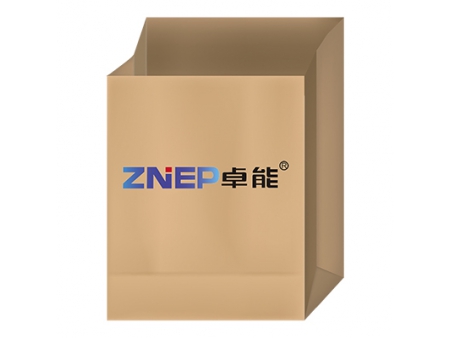
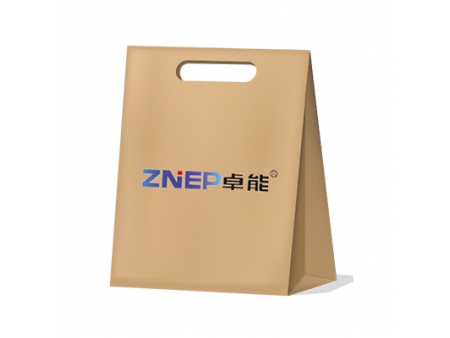
Model | ZD-F350S | ZD-F450S |
Roll paper width | 420-1090 mm | 670-1290 mm |
Cut off length | 260-530 mm | 260-530 mm |
Finished paper bag width | 130-350 mm | 240-450 mm |
Bag bottom width | 65-180 mm | 80-180 mm |
Paper gram | 60-150 g/㎡ | 70-150 g/㎡ |
Paper patch width | 100-150 mm | 100-150 mm |
Paper patch length | 50-100 mm | 50-100 mm |
Paper patch gram | 80-200 g/㎡ | 80-200 g/㎡ |
Max. dia. of roll paper | φ1500 mm | φ1500 mm |
Inner dia. of roll paper | φ76 mm | φ76 mm |
Max. production speed | 150/200 bags/min | 150/200 bags/min |
Total power | 28 kw | 28 kw |
Weight | 12000 kg | 13000 kg |
Overall dimensions(L*W*H) | 14000*3300*1900 mm | 14200*3500*1900 mm |
All processes can be made in one bag making machine to form the paper bag, from the paper roll, printing, side gluing, paper patching, tube forming & cutting, handle hole cut, bottom creasing & gluing and forming to bags collection in the control of seven Mitsubishi servo motors imported from Japan to ensure the high precision and stability, simple maintenance and high efficiency.
- Roll Feeding
- Patch Gluing
- Paper Patch Pasting
- Side Gluing
- Tube Forming
- D Handle Die-Cutting
- Tube Cut-off
- Creasing
- Bottom Folding
- Bottom Gluing
- Bottom Forming
- FEEDING UNIT
The roll paper fixed on the air expanding mandrel can be fed by swing arm which is equipped with lifting hydraulic system. With an alarm function, the feeding unit will sound alarm when there is no paper feeding. Improved surface smoothness of the paper during the feeding is achieved due to the web guide and uniform tension control. Paper rolls can be easily changed by pressing a button.
- PATCHING UNIT
This unit adopts an abreast double-knife to ensure the synchronization of the film patch or paper patch. Gluing, traction and cutting of the patch rolls are all controlled by servo motors. After putting the glue on desired locations and folding by a pneumatic roller, the system realizes the automatic functions of paper feeding, conveying, window gluing, film slitting and patching to produce the ready paper bags through a second roller mechanism.
- SIDE GLUING UNIT
A glue level sensor is used to detect the amount of glue left in the machine. The glue dispenser is used to apply adhesive to the desired locations of the paper.
- BAG FORMING UNIT
Form the paper with patches and side glue into the tube; and cut into separate pieces based on the settings. Afterwards, these separate tubes will be sent to the drum to open the four corners, then have the bottom glued and sealed, finally form the square shape.
- BAG COLLECTING UNIT
Compress the bags and outlet the bags. The number of paper bags can be processed and presented by the automatic collection and counting system.