Garage Door Roll Forming Line
Continuous PU sandwich panel line for insulated garage door
This garage door roll forming line is a continuous PU sandwich panel line that produces double-skinned sectional door panels with polyurethane insulated core. This garage door production line mainly consists of uncoiler, leveler, upper and lower roll formers, PU foam injection machine, hydraulic press, fly saw cutting system.
Samples of Finished Product
In the sandwich panel production process, PU foam is continuously sprayed under high pressure into upper and lower sheet metal profiles that are formed by upper and lower roll forming machines respectively. The PU insulated sandwich panel is then cut off to desired length via fly cutting saw prior to being discharged and collected.
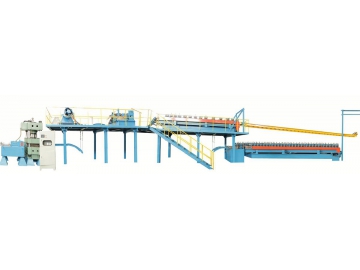
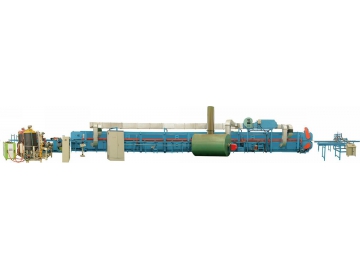
- Quick change system of roll forming machine enables forming rolls to be quickly and easily changed for producing different profiles.
- PLC control system adopts imported motion controller to guarantee high precision, and drive system utilizes only Siemens servo motors.
- The roll forming line is designed with gear transmission system, ensuring that the machine has high precision and long lifespan.
- Fly saw cutting system adopts hydraulic cutting method.
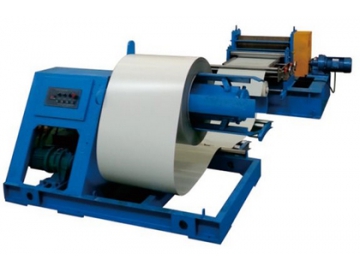
- Loading capacity: 5 tons
- Coil outer diameter: 1,100mm
- Coil inner diameter: 480-510mm
- Plate width: 1250mm
- Drive power: 5.5kW
- Hydraulic power automatic expansion to tighten the coil
- Hydraulic power (automatic coil tensioning): 5.5kW
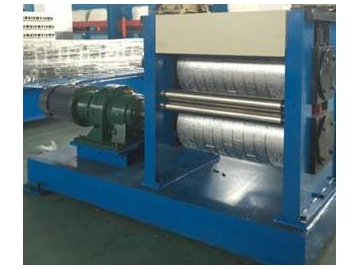
- Max. width of embossing pattern (normally wood grain pattern): 850mm
- Footprint size (D×W×H): 1770×3087×1500mm
- Motor power: 5.5kW, 50HZ/60HZ, 220V/380V
- Panasonic speed control (in freestanding cabinet): 8-15m/min
- Embossing roller size: Ø340×1000
- Rubber drive rollers at feed station
- Pattern matches the thickness of the sample provided
- Runout table rollers are mounted on a main frame of 500mm
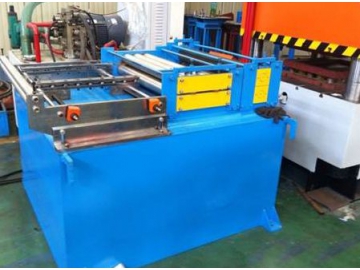
- The leveler adopts leveling rollers for precision leveling of sheet metal
- The feeding section is driven by servo motor, and uses rubber rollers for feeding
- Gear transmission method
- Motor power: 1.5kW
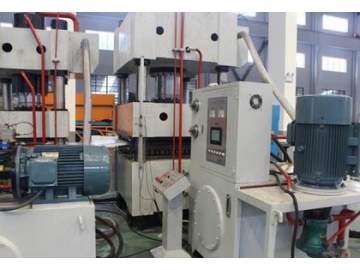
- Nominal pressure: 2000kN/3150kN
- Master cylinder stroke: 400mm
- Cylinder pressure: 1000kN/630kN
- Cylinder stroke: 100mm
- Max. opening (daylight): 500mm
- Working area: 1200mm×1300mm / 950mm×950mm
- Motor power: 15kW/22kW
- Hydraulic motor: 15kW/22kW, 220V/380V, 50HZ/60HZ, 3 Phases, Siemens brand
- Hydraulic pump: Yuken brand Taiwan
- Hydraulic valve: Rexroth Germany
- Hydraulic cylinder: China
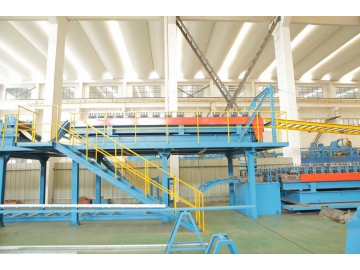
- Forming stations: 18 stations, cast steel structure
- Forming rolls: CR15 steel, HRC60 hardness, chrome coated (0.03-0.05mm), strength of 800Mpa
- Shaft: 60mm diameter, #45 steel, quenching hot treatment, main shaft strength of 650Mpa
- Bearing brand: FAG Germany
- Main motor: 7.5kW×2 (two motors), 220V/380V, 50HZ/60HZ, 3 Phases (Siemens brand)
- Gear transmission system
- Automatic width adjustment with servo control
- Final product width: 300-620mm
- Final product thickness: 40-55mm
- Applicable material: color coated steel sheet of 0.45 to 0.65mm in thickness
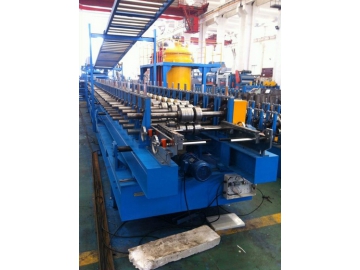
- Forming stations: 25 stations, cast steel structure
- Forming rolls: CR15 steel, HRC60 hardness, chrome coated (0.03-0.05mm), strength of 800Mpa
- Shaft: 60mm diameter, #45 steel, quenching hot treatment, main shaft strength of 650Mpa
- Bearing brand: FAG Germany
- Main motor: 7.5kW×2 (two motors), 220V/380V, 50HZ/60HZ, 3 Phases (Siemens brand)
- Gear transmission system
- Automatic width adjustment with servo control
- Final product width: 300-620mm
- Final product thickness: 38-76mm
- Applicable material: color coated steel sheet of 0.45 to 0.65mm in thickness
- Conveyor type: roller conveyor
- Roller diameter: Ø60
- Roller length: 1200mm
- Conveyor frame: channel steel and steel plate
This system is used to maintain a precise and uniform temperature of the upper and lower facing layers, thus achieving a homogeneous foam reaction as well as an excellent bonding between foam and facing layer.
- Welded steel base frame features protection grille which is lockable and thermally insulated
- Adjustable roller bars support the upper and lower formed sheet
- Top and bottom supports hold the infrared modules
- Infrared modules have heater steel sheet hoods to contain infrared heater tubes and fans
- Twin-tube quartz glass infrared heater, gold-plated
- PLC temperature control
- Touch screen brand: Delta
- PLC brand: Siemens
- Inverter brand: Siemens
- Low-voltage electrical components brand: Schneider Germany
- Encoder brand: Omron
- Sensor brand: Balluff B F
①Uncoiler→Embossing Machine→Upper Roll Forming Machine→Pre-heating System→High Pressure PU Foaming Machine→Double Belt System (Continuous Press) and Side Block Feeding Machine and Heating System (for Double Belt)→Scanning Machine→Fly Saw Cutting System→Automatic Runout Table
②Uncoiler→Embossing Machine→Servo Driven Automatic Feeding System→200Ton Hydraulic Press →300Ton Hydraulic Press →Preheating System→High Pressure PU Foaming Machine→Double Belt System (Continuous Press) and Side Block Feeding Machine and Heating System (for Double Belt)→Scanning Machine→Fly Saw Cutting System→Automatic Runout Table
The polyurethane foaming machine has pump for polyurethane and isocyanate, adjustable to double length and line speed
- Foam pressure: 220bar (max.)/ 60bar (min.)
- Max. viscosity: 3.000mPas
- Length of double belt system: 18m
- Working height of lower belt: 1300mm
- Slat width: 900mm (upper)/900mm(lower)
- Number of slats per belt: 260
- Number of hydraulic cylinders: 6 pairs
- Lifting stroke of upper belt: max. 380mm
- Foaming pressure: max. 0.4bar
- Lifting time of upper belt: approx. 2min
- Power required for A.C. drive: approx. 2×12kW
- Power required for hydraulic unit: approx. 7.5kW
- Oil reservoir: approx. 160L
- Mechanical speed: 2m/min-12m/min
- Slat temperature: max. 60°C
- Temperature accuracy: ± 3°C
- Ambient temperature for production: 15°C to 35°C
- U-value of housing: 1W/m²K
- Heat-up time from 20°C to 40°C: approx. 2 hours
- Circulating air volume: approx. 2×8000m3/h
- Required heating power: 2×80kW
- Required hot water circuit pump:2×6.5m³/h
- Required hot water in-feed temperature: 110°C
- Required hot water return temperature: 90°C
Twin diagonal cross cutting saw is provided to cut the panel with two saw blades.
- Working height: 1300mm
- Length: 3000mm
- Width: 2500mm
- Panel width: max.650mm
- Diameter of saw blade: 500mm
- Drive speed: 700-1.500rpm
- Cutting accuracy: ±2mm
Huazhong is committed to the innovation of roll forming machines and helping customers lower their costs and stay ahead in their competitive market.