Non-PVC Infusion Bag IV Solution Production Line
The SR series non PVC infusion bag IV solution production line is our new generation soft bag IV solution production line. It is the result of our years of experience and built based on domestically and internationally advanced technologies. The production line can automatically finish such procedures as word printing, bag making, filling and sealing.
- The non PVC infusion bag IV solution production line provides simple, reasonable structure, reliable performance and high efficiency. In fact, it can produce 12000 single chamber or 7000 multi chamber soft bags every hour.
- Thanks to the patent design, the production line realizes the integration of bag making, filling and sealing, with a length shortened by 1/3.Accordingly, the workshop area and air conditioner purification area are greatly reduced, which results in lower investment cost and operating cost. 3. It achieves 100 % utilization of package materials, reducing the waste of resources.
- The soft bag IV solution production line adopts multi-language touch screen operation. Parameters like time, temperature, pressure and filling quantity can be set and monitored by the computer.
- The machine has a strong storage capacity. This enables users to previously store the actual welding parameter, so it can be used directly when the package material is changed.
- Users can set the production line to start up automatically, so as to warm up the machine. This helps guarantee enough running time.
- The filling system uses Coriolis mass flowmeter which contributes to wide range of filling quantity and high filling accuracy. It can also realize CIP/SIP.
- The use of world renowned brand key components like servo system, PLC and pneumatic elements helps ensure the smooth, reliable running of the machine.
Our non PVC soft bag IV solution production line is suitable for automatic filling of 50 ml to 5000 ml conventional infusion, special infusion, parenteral nutrients, dialysis fluid, antibiotic and special medicine.
The production line offers many great functions. It will automatically stop when there is no film, no bag mouth, no color ribbon, or the pressure is beyond allowed range. In addition, the production line will not start up if the temperature doesn't reach the set value. Moreover, if there is no bag, it will not perform filling, cap picking and sealing operations.
Type | SRD1A/1200 | SRD2A/2500 | SRS2A/2500 | SRD3A/3800 | SRS3A/3800 |
Max. Capacity | 1200bags/h | 2500bags/h | 2500bags/h | 3800bags/h | 3800bags/h |
Bag specification | 100 ml, 250 ml, 500 ml | ||||
Qty/cycle | 1 | 2 | 2 | 3 | 3 |
Interface Methods | Boat shape interface | Boat shape interface | Double tube interface | Boat shape interface | Double tube interface |
Color Ribbon Diameter | The standard ribbon with inner diameter of 3 inch and outer diameter smaller than 140 mm | ||||
Film Dimension | Standard film with inner diameter of 6 inch and outer diameter smaller than 600 mm | ||||
Printing | Hot sheet thermoprint; single color; production date, validity and approval number are simultaneously printed and easily changed。 | ||||
Power Source | 3 Phases 380V 50Hz | ||||
Power | 8 kW | 22 kW | 22 kW | 26 kW | 26 kW |
Compressed Air Pressure | Dry and oil free compressed air, the cleanness in 5 μm, the pressure is over 0.6 Mpa. The non PVC infusion bag IV solution production line will automatically stop and give warning signals when the pressure is too low. | ||||
Compressed Air Consumption | 1000 L/min | 2000 L/min | 2200 L/min | 2500 L/min | 2600 L/min |
Clean Air Pressure | Air with over 0.4 Mpa pressure and 0.22 μm cleanliness | ||||
Clean Air Consumption | 500 L/min | 800 L/min | 600 L/min | 1000 L/min | 800 L/min |
Cooling water pressure | >0.5 kgf/c㎡ | >0.5 kgf/c㎡ | >0.5 kgf/c㎡ | >0.5 kgf/c㎡ | >0.5 kgf/c㎡ |
Cooling water consumption | 100 L/h | 150 L/h | 100 L/h | 200 L/h | 150 L/h |
Nitrogen Consumption | It can be protected with 0.6 Mpa nitrogen according to special requirements. The consumption is below 45 L/min | ||||
Running Noise | < 75 db | ||||
Room requirements | Temperature of the environment: 26 ℃ ,humidity: 45 %-65 %, max. 85 % | ||||
Overall size | 4.2 m *2.1 m*2.1 m | 5.6 m *2.1 m*2.1 m | 8 m *2.97 m*2.1 m | 6.5 m *2.35 m*2.1 m | 9.8 m *2.97 m*2.1 m |
Reference workshop dimensions | 5.2 m *4.1 m*2.4 m | 6.6 m *4.1 m*2.4 m | 9 m *5 m*2.4 m | 7.5 m *4.5 m*2.4 m | 11 m *5 m*2.4 m |
Weight | 3.5 T | 6 T | 7 T | 7 T | 8.5 T |
Auxiliary equipment: soft bag dryer, leak detector, conveyer, pillow packing machine, case packer, sealing machine |
Type | SRD4A/5000 | SRD4A/5000 | SRD6A/7500 | SRS6A/7500 | SRD12A/15000 | |
Max. Capacity | 5000 bags/h | 5000 bags/h | 7500 bags/h | 7500 bags/h | 15000 bags/h | |
Bag specification | 100 ml, 250 ml, 500ml | 50 ml, 100 ml, 250 ml, 500 ml | ||||
Qty/cycle | 4 | 4 | 6 | 6 | 12 | |
Interface Methods | Boat shape interface | Double tube interface | Boat shape interface | Double tube interface | Boat shape interface | |
Color Ribbon Diameter | The standard ribbon with inner diameter of 3 inch and outer diameter smaller than 140 mm | |||||
Film Dimension | Standard film with inner diameter of 6 inch and outer diameter smaller than 600 mm | |||||
Printing | Hot sheet thermoprint; single color; production date, validity and approval number are simultaneously printed and easily changed | |||||
Power Source | 3 Phases 380V 50Hz | |||||
Power | 30 kW | 28 kW | 32 kW | 30 kW | 60 kW | |
Compressed Air Pressure | Dry and oil free compressed air, the cleanness in 5μm, the pressure is over 0.6 Mpa. The production line will automatically stop and give warning signals when it is too low | |||||
Compressed Air Consumption | 3000 L/min | 3800 L/min | 4000 L/min | 4200 L/min | 7000 L/min | |
Clean Air Pressure | Air with over 0.4 Mpa pressure and 0.22 μm cleanliness | |||||
Clean Air Consumption | 1000 L/min | 1000 L/min | 4000 L/min | 4200 L/min | 7000 L/min | |
Cooling waer pressure | >0.5 kgf/c㎡ | >0.5 kgf/c㎡ | >0.5 kgf/c㎡ | >0.5 kgf/c㎡ | >0.5 kgf/c㎡ | |
Cooling water consumption | 300 L/h | 250 L/h | 400 L/h | 300 L/h | 800 L/h | |
Nitrogen Consumption | It can be protected with 0.6 Mpa nitrogen according to special requirements. The consumption is below 45 L/min | |||||
Running Noise | < 75 db | |||||
Room requirements | Temperature of the environment: 26 ℃, humidity: 45 %-65 %, max. 85 % | |||||
Overall size | 8.5 m *2.7 m*2.1 m | 11.8 m *2.97 m*2.1 m | 9.9 m *2.55 m*2.1 m | 14 m *2.97 m*2.1 m | 9.9 m *4.4 m*2.3 m | |
Reference workshop dimensions | 10 m *4.7 m*2.4 m | 13 m *5 m*2.4 m | 11 m *5 m*2.6 m | 15 m *4.7 m*2.4 m | 11 m *6.5 m*2.6 m | |
Weight | 10 T | 10 T | 10 T | 12 T | 14 T | |
Auxiliary Equipment: soft bag dryer, leak detector, conveyer, pillow packing machine, case packer, sealing machine |
The soft bag IV production line is made up of two main parts, that is, bag making part as well as filling and sealing part. Specifically, it includes automatic film feeding unit, words printing unit, forming unit, tube port welding unit I and II, bag cooling and separating unit, tube port fixing clip reversing unit, tube port conveying unit, tube port preheating unit, filling pipeline, CIP/SIP system, bag pressing unit, cap sending set, heating set, emptying set, automatic control, and more.
The automatic film feeding is accomplished by a reeling frame. The bag film reel is designed to allow an easy change of the film rolls. The roll can be fixed on the reel by pneumatic clamps without needing any tools. The continuous and even film feeding motions are realized by an electric motor drive. The film is stored by a buffer roller and then stepwise fed to the operation stations. A sensor control ensures an even film motion from the beginning till the end of the bag-film roll.
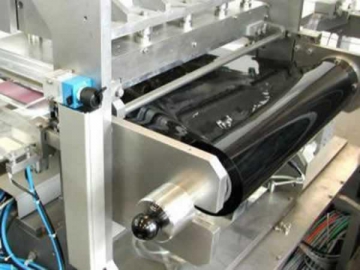
A hot foil printing device is used. Printing temperature, printing time and pressure are adjustable. An automatic print foil control ensures that the machine will stop when the foil is at the end or torn off. Tool less and easy print foil changes contribute to minimum downtime. Therefore the printing foil reels are provided with pneumatic clamps for quick and easy change. There is an additional device which ensures the printing foil and the bag film will not stick together after printing. All qualified printing foils can be printed and all colors are available. Simple tools are needed for changing of printing plate. In fact, this can be achieved through simple twist by a clamp device.
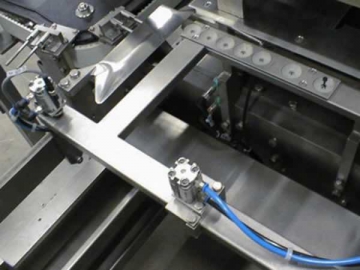
An electric motor driven linear gear unit is used to perform film transfer. The film is held by pneumatic film clips during the transfer. When the film is fed in, the two film layers are then being opened.
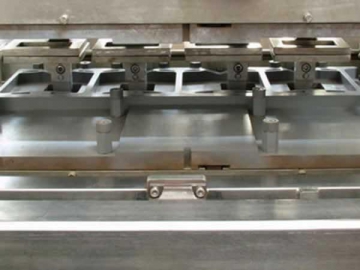
This station is used for adhering the ports to the bag film, welding and cutting the outer contour of the bags. The welding is performed by exchangeable welding tools which are provided with heating cartridges so as to produce the required welding temperature. Welding time, welding pressure and temperature are adjustable. In order to guarantee a permanently correct welding process, the welding temperature is verified within a defined minimum or maximum range by the PLC control unit and temperature sensor. When the welding temperature is less than or higher than the defined minimum or maximum range, the machine will stop and an error message is displayed in the control panel at the same time.
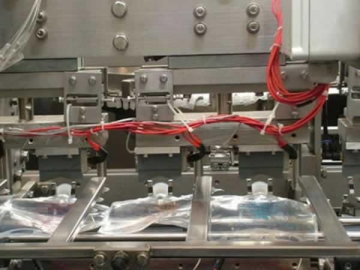
The tube port welding is done by an appropriate welding device. The station incorporates a min. or max. welding temperature control for an optimum welding temperature. If the welding temperature is beyond allowed range, the machine will stop for quality aspects.
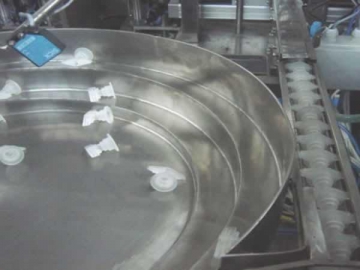
The tube ports are finally welded by an appropriate welding device. Meanwhile, there is a special gripper system that takes over the cut edges of the bags and collects them into a tray.
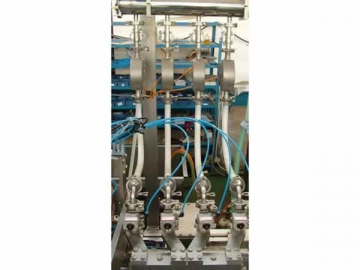
The filling operation is performed by 4 mass flow meter filling systems with GEMU diaphragm valves, product distribution and connecting hoses and micro processor control unit, which is located in the main switch cabinet. The filling system is lowered towards the bag by means of a pneumatic cylinder and can be easily adjusted for different filling volumes. The filling volume range is from 100 ml to 10 L. The filling tube port is centralized by a conical centering device.The filling systems are designed to be sterilized inline. No part has to be dismantled.
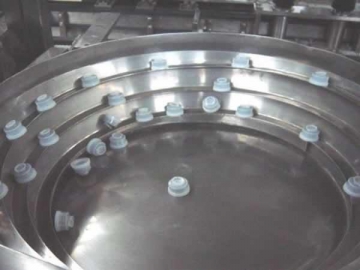
The station is including an automatic cap feeding and transport system, a port and cap heating device and an air exhaust system. The caps are automatically fed properly from a hopper, following vibrator bowls and linear cap chute. There are four grippers at the longitudinal side of the system. They catch the caps and bring them into position atop the bag ports. Then the heater tongues move between caps and ports so as to prepare them with non contact heating for the sealing operation. In order to minimize the residual air in the bag, the air exhaust operation is accomplished at the same time. Therefore, the filled bags are pressed until they reach a fixed level. Finally, the heater tongues move back and the caps are put onto the ports. If the bag has not been filled, it will not be sealed. The station also incorporates a cap control. Bags without a cap will be identified as rejects.
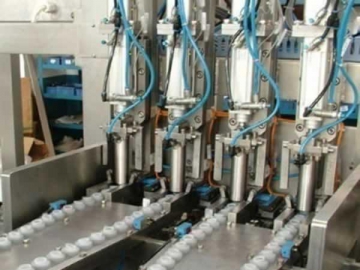
The finished bags are taken out by gripper system and removed from the machine to the output conveyor belt. Bags identified as bad bags are rejected automatically and drop into a collecting tray.
IVEN Pharmatech is a professional non-PVC infusion bag IV solution production line manufacturer, based in China. We offer a broad range of products, including linear labelling machine, ultrasonic bottle washing machine, carton elevator, and more.